Lean Manufacturing has become very popular in recent years, as a result of the initial success of its methods in the Japanese automotive industry and a climate of fiscal restraint, where the idea of “lean” was obviously widely accepted.
With the goal of making things easier and more efficient, Lean Manufacturing was first seen as the natural enemy of heavy and expensive IT systems, a category in which the systems of the Manufacturing Execution System could be wrongly classified. But are Lean and MES really enemies?
What is lean manufacturing?
Lean Manufacturing is based on eliminating waste in production processes.
The objective is to gradually eliminate the “no value added”, to give the manufacturing workshop greater flexibility.
More specifically, the Lean approach aims to create processes that will require less human effort, less space, less capital and less time to create and manufacture the product to make products and services less expensive and with fewer defects (compared to a traditional organization).
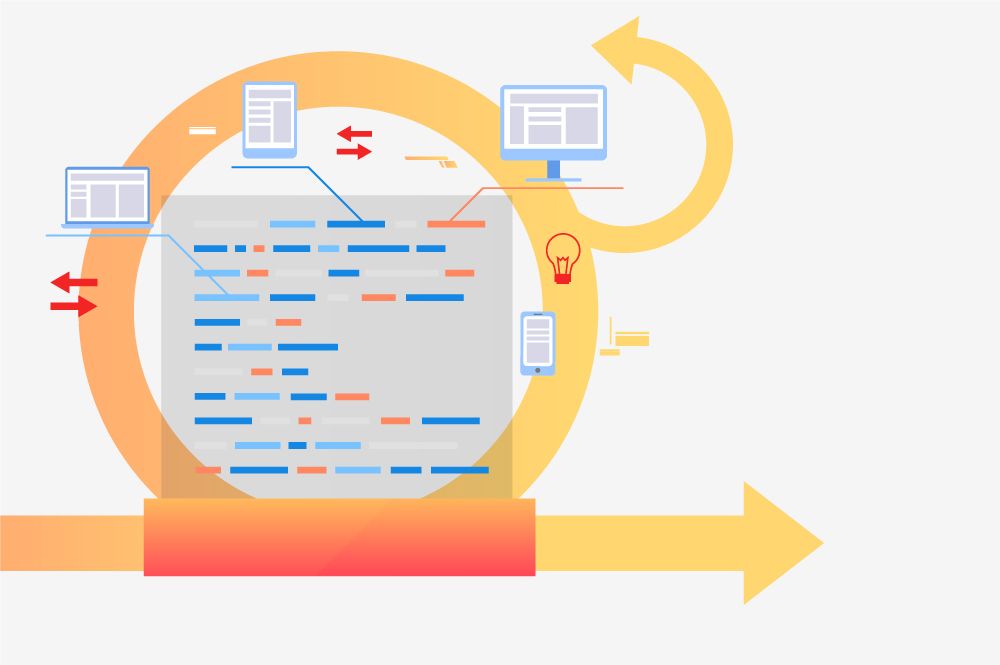
What waste?
Seven types of waste can be identified:
- Overproduction
- Over-stocking or unnecessary stock
- Unnecessary transport and travel
- Over-processing or unnecessary processing
- Unnecessary movements
- Errors, defects or scrap
- Waiting times and deadlines
The 5S method
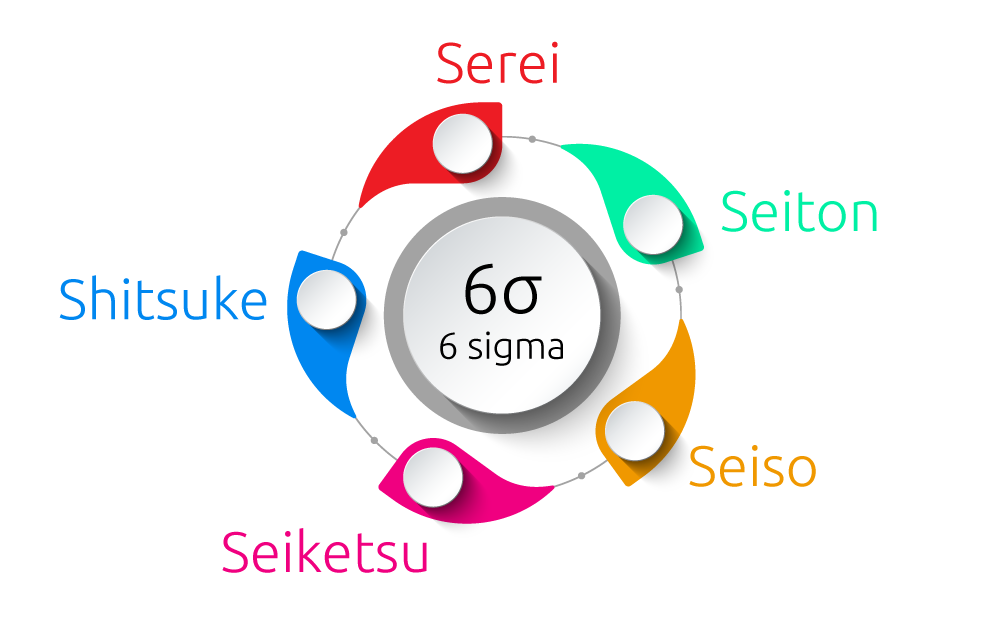
The term Lean was created to describe the TOYOTA model in the late 1980s by a research team led by Jim Womack, a PhD graduate from MIT.
The 5S method, which is no more than a workplace organization method, has been developed within the TOYOTA production system:
- Seiri (sort)
- Seiton (set in order)
- Seiso (shine)
- Seiketsu (standardize)
- Shitsuke (sustain)
It has several objectives:
- Eliminate unnecessary items from the workspace
- Arrange items so that they are easy to use, find and put away
- Keep the items and work area neat and clean
- Create a consistent approach to tasks and procedures
- Make a habit of maintaining the correct procedures
The whole system also allows:
- To improve the working conditions and the morale of the staff (it is more pleasant to work in a clean and tidy environment)
- To reduce time and energy costs
- To reduce the risk of accidents and/or health hazards
- To improve the quality of production
- To improve production management
Did you say Kaizen?
The word Kaizen is the fusion of two Japanese words that mean "change" and "good" respectively. The current English translation is "continuous improvement". It is in fact the name of a quality management method, which implements specific, successive, simple and inexpensive improvements.
But it is also, and above all, a state of mind that requires the involvement of all actors: coming together to change the world and telling everyone about it!
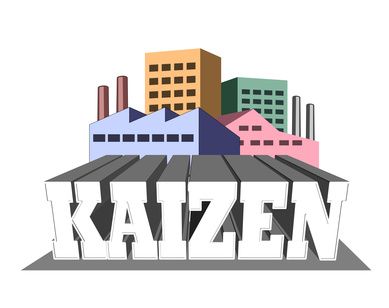
Lean Manufacturing and its limits
In recent years, after going beyond its original framework - the organization of production - Lean Manufacturing is now perceived as a relevant alternative against all types of inefficiency.
Applying Lean principles, including the continuous improvement of the system, requires profound changes in organizations.
Problem solving as closely as possible to the field, involving both operational and managerial staff, is a first major change, since change is perceived in large organizations as something that follows the chain of command from top to bottom, where little autonomy is left to those in the field in terms of taking initiatives.
Finally, there are those who question this method by pointing to the deterioration of working conditions: an in-depth search for profit by reducing waste could prove dangerous for workers' health: by removing unnecessary gestures, lean management intensifies work efforts and can generate musculoskeletal disorders.
Lean Manufacturing & MES synergy
Real-time monitoring of production
MES naturally provides real-time monitoring of production.
It also makes it possible to capture and qualify management data and make available all the elements necessary for operational production (documentation, planning, etc.) in an appropriate and productive way.
For a Lean approach to be effective, it is necessary to follow the measurements, trace them within the expected time frame and have a analysis and control of the production data in real-time. The frequency of data collection permitted by an MES tool will increase efficiency and solve problems quickly.
Establishment of reliable and effective indicators
An MES tool complements a Lean approach by supporting it, strengthening it and implementing the best practices, measuring performance and improving the process by eliminating waste. It will ensure the success of a continuous improvement approach by accelerating the Lean Manufacturing initiatives.
In order to implement an effective Lean approach, there is a need for reliable data that is properly collected and measured. That is why an MES tool is so important. Manual data collection is rarely effective.
Support for various components of Lean Manufacturing
A common implementation will also make it possible to carry out the different steps of Lean Manufacturing (calculation and follow-up of OEE, 5S approach, Sigma, Smed, etc.).
By planning the various stages of waste reduction, cost reduction and quality management, processes can immediately be implemented in a coherent manner, and above all, maintained over time.
Areas for improvement can be clearly identified from one machine to another, from one workshop to another and from one plant to another by monitoring operations and establishing Key Performance Indicators (KPI).
Help with change management
Finally, an MES tool, by automating the improvement of the process, will help manage change and adopt it gradually until getting the support of the staff. Operators are informed in real time of any malfunctions and can react immediately :
They are then in a position to take appropriate corrective action.
In the same way, in the current context in which companies must pay more and more attention to the environmental consequences of the processes used, the products and services offered, where energy costs and the price of materials are constantly increasing, the manufacturer must adopt effective sustainable development strategies : a Lean approach combined with an MES tool will enable the manufacturer to remain competitive.
Conclusion
MES and Lean are thus complementary and not independent as some make them out to be. An MES tool will then play a key role in the success of the Lean Manufacturing process.
Guaranteeing continuous improvement, reduction of waste and improved response times, an MES tool undoubtedly adds value : time saving, availability of increased resources to maintain and optimize the performance of operations within the company.