The debate on the dividing line between ERP and MES, which indeed is variable depending on the processes and even the industrial’s choices, scarcely go beyond arbitrage duties on the management of units’ stocks and the products manufacturing recipes.
In 80% of all cases, ERP will bring to the MES a manufacture order list that it would have to execute by controlling the operations proceedings and their traceability, giving back to the ERP the raw materials consumption, the production performance and the quality of manufactured products.
This work of clarification has been more scarcely done on the dividing line between SCADA and MES, the reason why is: the very existence of this dividing line is a real mystery.
The pyramids' secret
To unravel this mystery, we have to be aware of the power exerted (and still exerts) by a very consensual representation in the automation world and that is the CIM pyramid (see the figure at the opposite)
The CIM (Computer Integrated Manufacturing) had known a wide spread during the eighties. What is kept in mind is the pyramidal representation of the different material and software layers, which CIM implies in the production’s digital architecture of a company.
The original CIM diagram doesn’t mention the SCADA positioning (these programs were nascent when the CIM was put in place). It could be tempting to add it as an additional layer, and to characterize more precisely each layer, which gives the following representation.
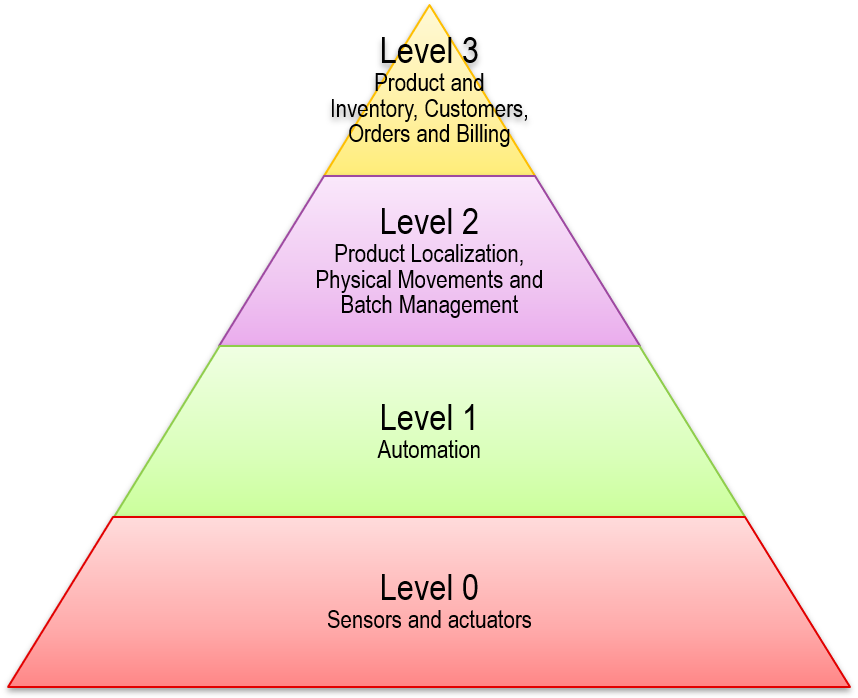
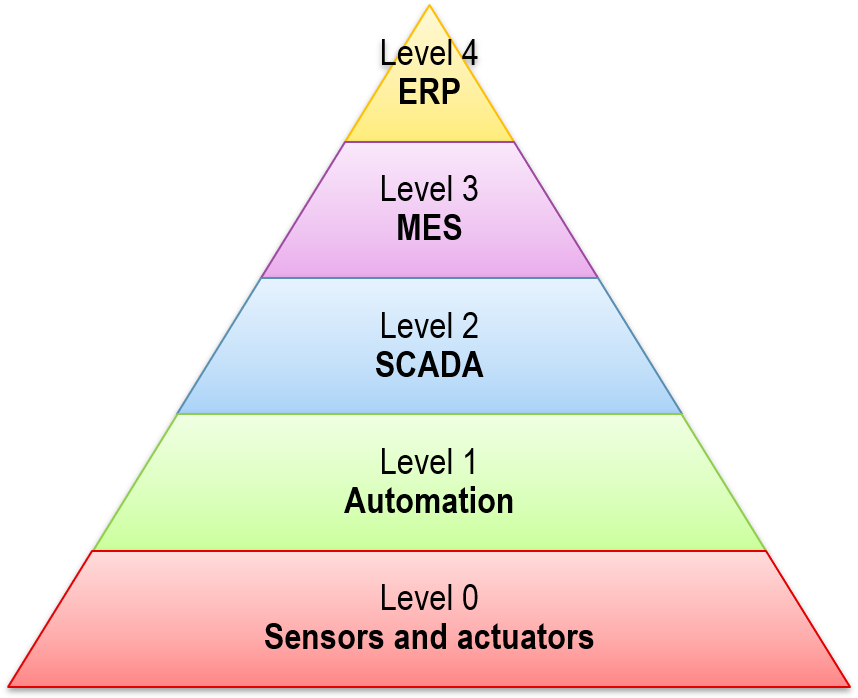
This pyramidal representation implicitly relies on several hypotheses, even if these are never expressed very clearly.
The first one is the functional hierarchy whose effect is reinforced by the representation. It implies that we go from the simplest functions (at the bottom of the pyramid) to the most complex ones (at the top of the pyramid). The second hypothesis – it is more likely the most important – is that every functional block can only adjoin with the one right above it and the one right below it. This last hypothesis is at the same time stated historically by an analogy with the traditional management structures but also by the existence of material communication types really different at each level: during the eighties, sensors’ networks, automatons’ networks, and computing networks were of different types, unable to coexist on the same physical material.
Nowadays, we don’t assume that the intelligence is essentially concentrated at the top of pyramids, and especially Ethernet and TCP/IP established themselves as basic universal layer for most networks, whether for sensors or actuators’ networks, automatons or computing networks, or even the worldwide internet connection. But, without affirming that CIM pyramid got split, at least it is possible to say that this representation is less naturally obvious than during this period.
Nevertheless, the pyramids’ “secret” is to convey furtively a division which doesn’t necessarily correspond to a functional reality, neither to a current technical constraint nor to the reality on the field (as we will see it later).
But let’s see first if ISA, the main contributor to the analysis work of MES through ISA-95 standard, defines better SCADA and MES areas…
MES and SCADA according to ISA's work
First, let’s remember that the first objective of ISA- 95 has been to define an exchange mode between the MES and ERP. The first positive consequence is that it justifies the existence of these two programs within the whole production architecture.
In the functional positioning of MES, ISA didn’t take the pyramidal representation of CIM; however they kept the levels, appointing the level 4 to the ERP and the level 3 to MES, it is close to the representation we have made in Figure n°2.
The global drawing, which highly distinguishes in the lower levels the type of processes, is represented by figure n°3. At first glance, even though the representation is different, it seems like the CIM pyramid extend to SCADA, even dated, remains relevant. But, is it the case?
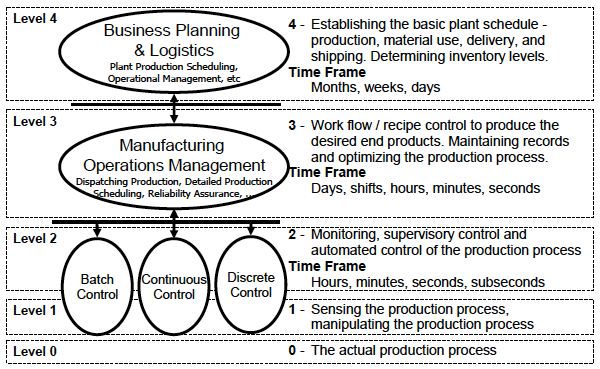
Figure 3 - Découpage fonctionnel ISA-95 / IEC 62264
By going further in the figure details, we observe that the ISA-95 doesn’t identify more clearly the first versions of CIM and SCADA positioning. SCADA is literally the acronym for Supervisory Control And Data Acquisition. If Monitory Control and Supervisory Control are considered like being in level 2, Data Acquisition (the D.A of SCADA) and Recipe Control, often considered as SCADA functions, are bound with level 3 in ISA-95. Level 2 is more considered as the one for “automatisms”.
Plus, if we find, especially in the part 2 of standard, long development on the establishment of exchanges patterns between MES and SCADA, we would look in vain for a definition of exchanges between MES and SCADA. How is it possible to explain this absence?
The reality on the ground - parallel lives
To understand fully the reality on the ground, another presupposition from the CIM pyramid has to be taken into account: CIM developers get carried away in their idea of industrial facilities with complete automation, therefore manual operations don’t appear, even if they are numerous and dominating in this type of industry. Yet, the SCADA automatons and programs haven’t been conceived to manage manual operations. For lack of anything better, for a long time the industrials considered that a SCADA was needed to make Man-Machine Interfaces (MMI), but actually this function doesn’t belong to any software.
Therefore in practice, when the MES programs were first released, they take into account directly manual operations, generally through data entry interfaces. To make information gathering and traceability easier, devices such as bar code readers and tag printer are managed by the MES software either directly or through automatons, but mostly never through the supervision software. Presenting SCADA as an intermediary stage between the “ground” and the MES through automatisms doesn’t really match with reality. In practice, supervision and MES follow completely different paths (parallel lives). Furthermore, the tools are often linked to different cultures: supervision developments reflect an “automatisms” vision of the production, really oriented “bits and words”, that is “basic input/output system”, whereas the MES developments reflect an “operational” vision, more structured and generally more “computing”. Thus, not any structured exchanges has been really defined between SCADA and MES, it is simpler for MES programs to gather the data at the roots. The functional diagram of ISA-95 also highlights that MES works on the same time scales as SCADA with only few specific exceptions. The figure n°4 represents the real positioning of SCADA and MES.
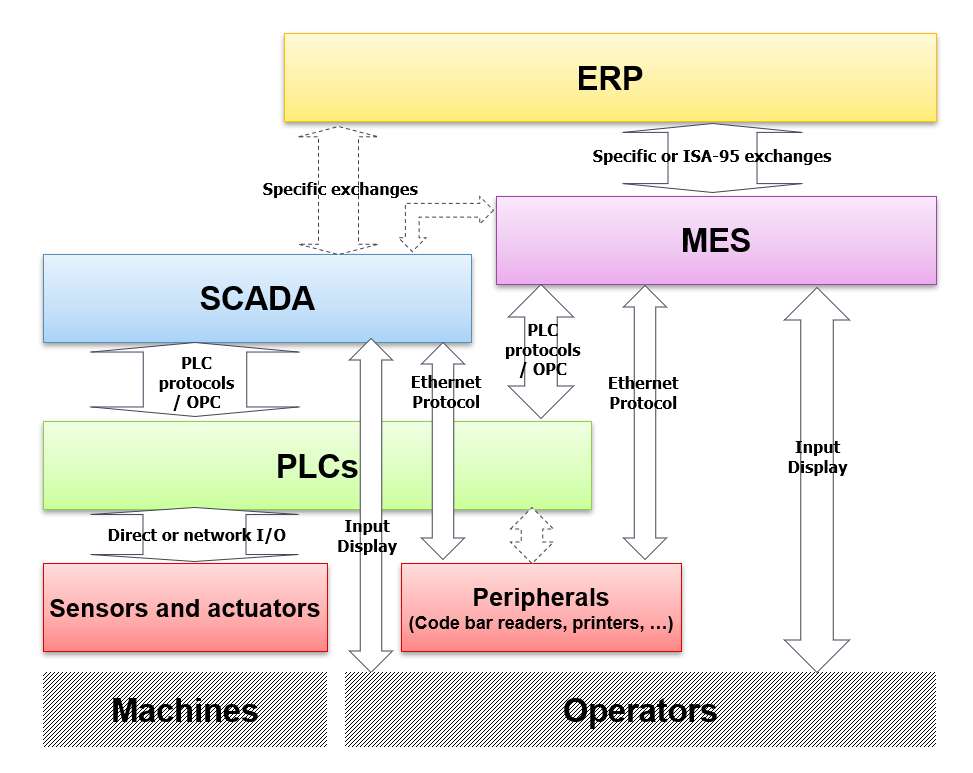
Figure 4 - Organisation fonctionnelle réelle Automation/SCADA/MES
This figure demonstrates a bigger confusion on SCADA and MES roles. A confusion that the pyramidal representation doesn’t foretell and which explain a great part of the questions the industrials could ponder on the role played by each of these both programs. The data acquisition and a part of the operations control are directly in duplication between the two programs’ blocks, whose screens are presented at their sides to the same operators.
Sometimes, the parallelism even goes till archiving, each of both tools storing nearly the same data in different systems. In such confusion, it is possible to find logical asking the supervision solution’s integrator to connect himself directly to the ERP, which doesn’t necessarily mean, as assumed before, that the supervision tools are equipped of MES functions! The integrators are led to make important specific developments, difficult to set up and to maintain, and generally diverted by the constraints of ISA-95 good practices software.
To avoid this confusion, it is better to gather SCADA and MES within a same software platform, sharing at least common functions between these software: communication with automatons, communication with production peripherals, data acquisition and archiving, man-machine interface …etc. A modular approach will enable the industrials to adapt the functional perimeter to their own needs. The organization is then the one in the Figure 5, clearer and more efficient.
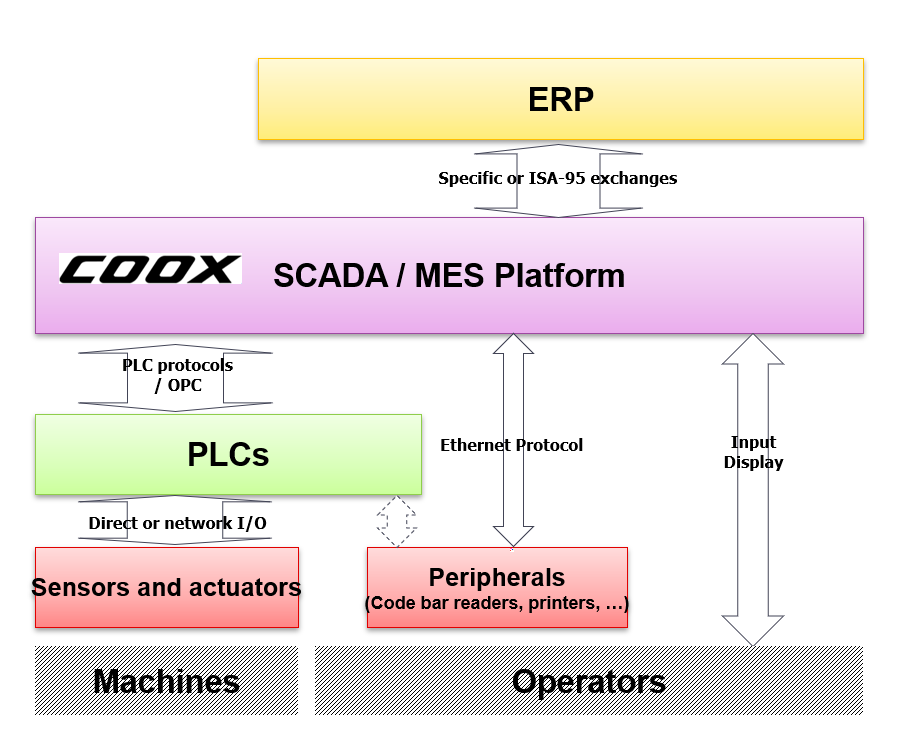
Figure 5 - Organisation fonctionnelle d'automation avec fusion SCADA/MES
Conclusion
SCADA and MES, which often share roles within an industrial facility, collaborate in a less clear and efficient way that the pyramidal representation inspired from CIM imply. The ground reality shows that MES scarcely interplays with supervision tools. The coexistence of both tools correspond more to an historical development rather than a natural collaboration between both programs. On the contrary, a merger of these tools within a same software platform represents an important benefit for the industrial in terms of simplicity and deployment cost, applications maintainability and operators’ efficiency.