Some customers ask themselves if ERP (Enterprise Resource Planning) and MES (Manufacturing Execution System) are playing the same role. They thus challenge the opportunity to install an MES system after their ERP system has been installed. Actually MES systems have been designed to cooperate with ERP systems.
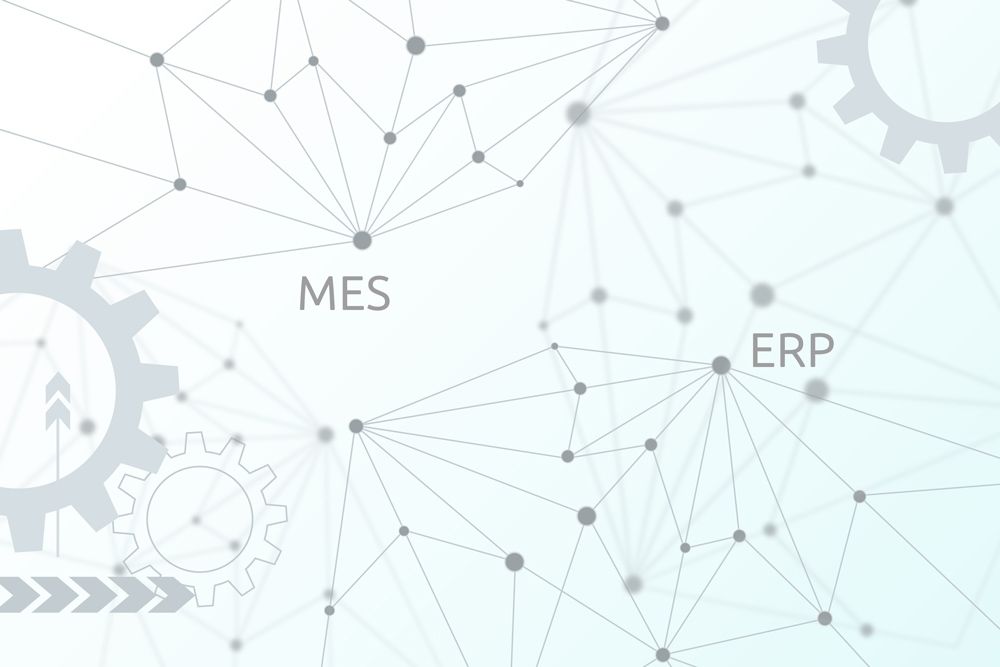
The key role of ERP in the entreprise
For quite an extended period, manufacturers focused on automating processes and improving productivity. Although some companies are only just beginning, many have set up high-level automation and supervision systems. Lately, large and small industrial concerns have made extensive investments in ERP systems for managing their business. ERP systems provide a “transaction-based” business intelligence tool for production planning and organization. ERPs offer high-level integration of Computer Integrated Manufacturing (CIM) across the enterprise and they have confirmed their role as a federating, multi-site corporate tool. But what matters for Production Managers is execution. The MES is designed for production managers, to deliver precise control of production and to drive progress in the production unit.
MES and ERP are complementary by nature
ERP and MES are complementary tools for ensuring free flow of manufacturing information, and leveraging it within the enterprise. The ERP and MES do not work on the same time scale: an ERP rarely works on periods shorter than a half-day, while the MES works either minute by minute, or over ten or twenty minute stretches. This different time scale tends to hide another, more important difference: the ERP is not designed to collect and process finely-meshed data in real-time. This fine mesh is necessary to control and coordinate processes with tight constraints concerning ᅠtraceability and performance improvement.
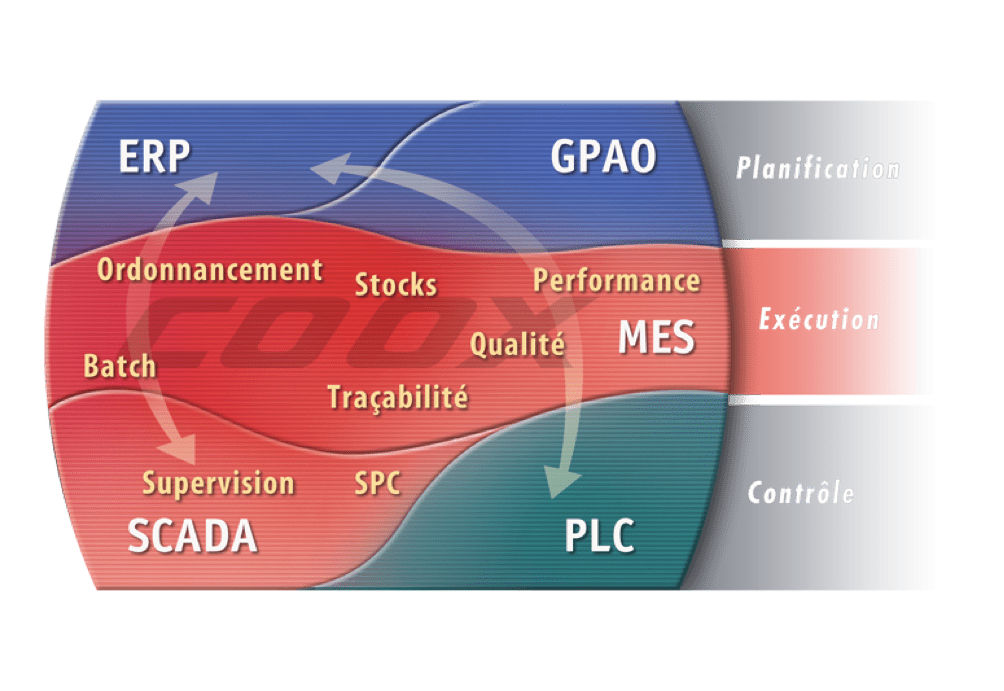
If no MES is available, the company itself must manufacture products using only the work order generated by the ERP. At the end of each work order, the company directly fills out a form managed by the ERP and used to collect all the data concerning the order: quantity actually produced, materials consumed with their source, test results, execution times and losses, scrap, etc. This requires very costly and unreliable data entry. Manufacturers are usually aware of this issue, and often request that the ERP system integrator develop "customizations" for collecting information at the various steps of the production process, synchronizing them, and forwarding the consolidated information to the ERP—in short, to develop a custom MES ! Is this the best way to run a business? Definitely not, given the limited number of possibilities, the upgradability issues, and the costs involved.
The MES organizes detailed production tasks and feeds information to the ERP
Today the complementary nature of the ERP and the MES is widely recognized, particularly by manufacturers who have been using an ERP for some time and have mastered the functional scope. Both proprietary standards (such as SAP XI) and open standards (such as ISA-95 part 5 and B2MML) are increasingly used for facilitating exchanges between these programs.
COOX features numerous exchange mechanisms compatible with your legacy ERP or CAPM solution. An ERP provides a “macro” view of many operations; by implementing a standard MES, you can more precisely organize those operations and run them without using an informal or paper-based process. The figure below shows a sample production recipe viewed by an ERP and by an MES.
Furthermore, in order for an enterprise to make the best of the ERP, the software must be fed a constant stream of data and information collected in the field. A standard MES solution provides operators, management, and the ERP with the quantities actually manufactured and scrapped, the traceability of both the process and the products, and performance levels. It provides real-time business management information and helps you fine-tune subsequent production schedules.
The MES is an information system focused on the factory and workshops, and the operations that take place there. It provides the means to unify cross-functional activities—production, quality control, maintenance, and processes—vital for managing and controlling manufacturing operations. The MES consolidates data and feeds the ERP; it is critical for efficient manufacturing.