Dans l’organisation fonctionnelle des différentes solutions logicielles intervenant dans la fabrication, le MES est classiquement situé au niveau 3, entre un niveau 2 reposant sur les opérateurs et/ou le contrôle-commande des machines et un niveau 4 tourné vers la planification, comme le rappellent les acronymes des principales solutions du niveau 4 : ERP = Enterprise Resource Planning, MRP = Manufacturing Resource Planning (voir figure 1).
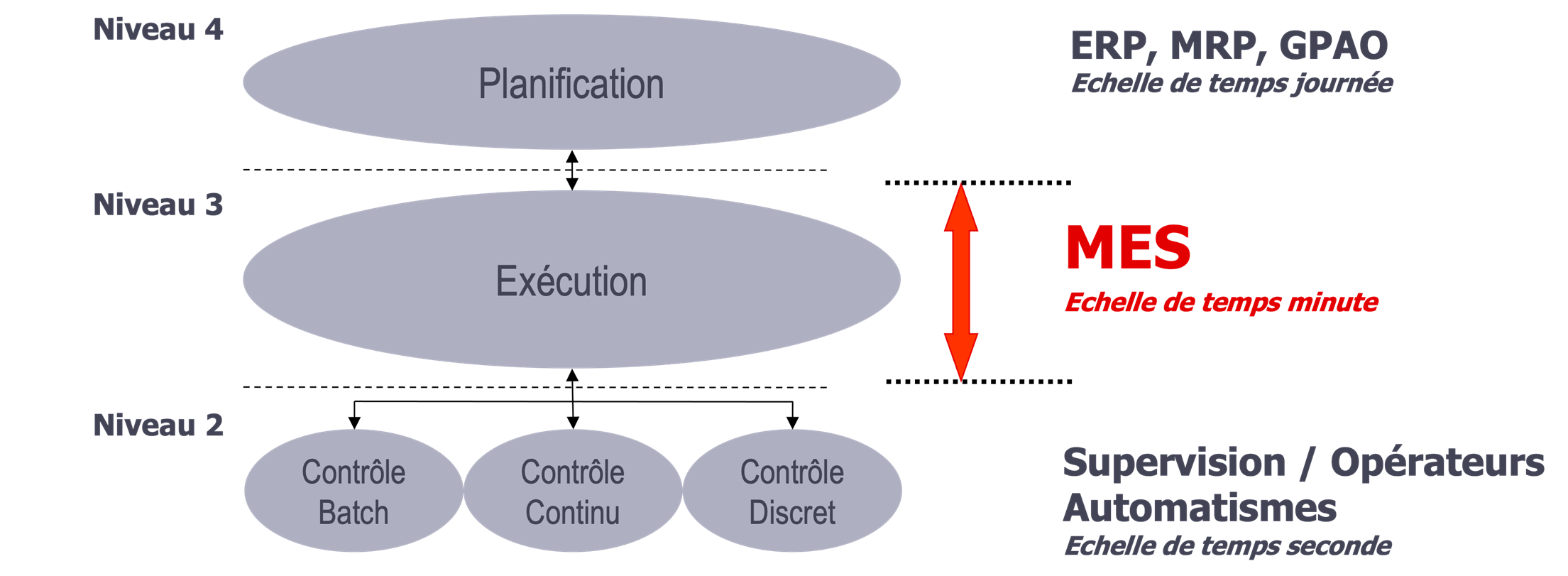
La planification : domaine de l'ERP ou du MES ?
Sur la base de cette répartition fonctionnelle, on aurait donc tendance à considérer que la planification n’est pas du domaine fonctionnel du MES, mais plutôt de celui de l’ERP.
Dans la pratique, la planification réalisée au niveau de l’ERP ne satisfait pas toutes les attentes de la production. En effet, l’ensemble des équipements de production n’est pas toujours connu de l’ERP de manière précise et dans ce cas les équipements d’exécution ne sont pas assignés. De la même manière, le personnel n’est pas assigné nommément aux ordres de fabrication. De ce fait, des contraintes effectives de disponibilité d’équipements ou de personnel ne sont pas prises en compte dans la planification.
Pour couvrir ce besoin, les industriels peuvent avoir recours à plusieurs types de solutions. Les versions « basiques » s’appuieront sur un planning mural à fiches cartonnées ou un tableau Excel. Techniquement simples, ces solutions sont toutefois très chronophages pour le responsable de la planification ou le responsable de production. A l’opposé, une offre de logiciels APS (Advanced Planning System) est disponible. Ces derniers utilisent différents types d’algorithmes (combinatoire, génétique, simplexe, …) visant à obtenir un ordonnancement optimal. Toutefois, ces outils requièrent un paramétrage exhaustif de l’ensemble des contraintes qui peut s’avérer délicat. Par ailleurs, si les conditions changent, le reparamétrage et le recalcul du nouveau plan peuvent être longs.
De manière générale, la planification réalisée au niveau de l’ERP est plutôt une planification « macro » : par exemple, les temps de pause sont intégrés
au global dans le temps de l’équipe sans les situer dans le temps à un horaire précis, les phases de réglage nécessaires sont traduites par une basse de la cadence moyenne prise en considération les calculs de charge des équipements, etc.
Par ailleurs, l’ERP ne remettra pas à jour en temps réel le planning si les cadences ne sont pas tenues, si des pannes ou des non-qualité affectent significativement la production ou en cas d’indisponibilité imprévue d’un personnel critique. Ces limitations concernant la planification mettent au jour un besoin de planification détaillée ou d’ordonnancement en temps réel des activités de fabrication.
Les logiciels de MES disposent souvent de capacités de planification détaillée offrant un excellent compromis entre ces deux extrêmes. Sans prétendre à l’obtention d’un optimum de la planification, ils pourront suivant les éditeurs, assister le responsable de la planification dans la prise en compte des contraintes telles que la capacité des équipements et la disponibilité des ressources de personnel. En fonction des informations disponibles dans l’ERP sur les dates d’approvisionnement des composants ou les dates d’expédition prévues, la date minimale de début et la date maximale de fin de chaque OF peuvent également être intégrées en tant que règles. Certains logiciels permettent également l’intégration au planning d’autres types d’ordres de travaux, comme des ordres de maintenance ou de nettoyage (voir figure 2).
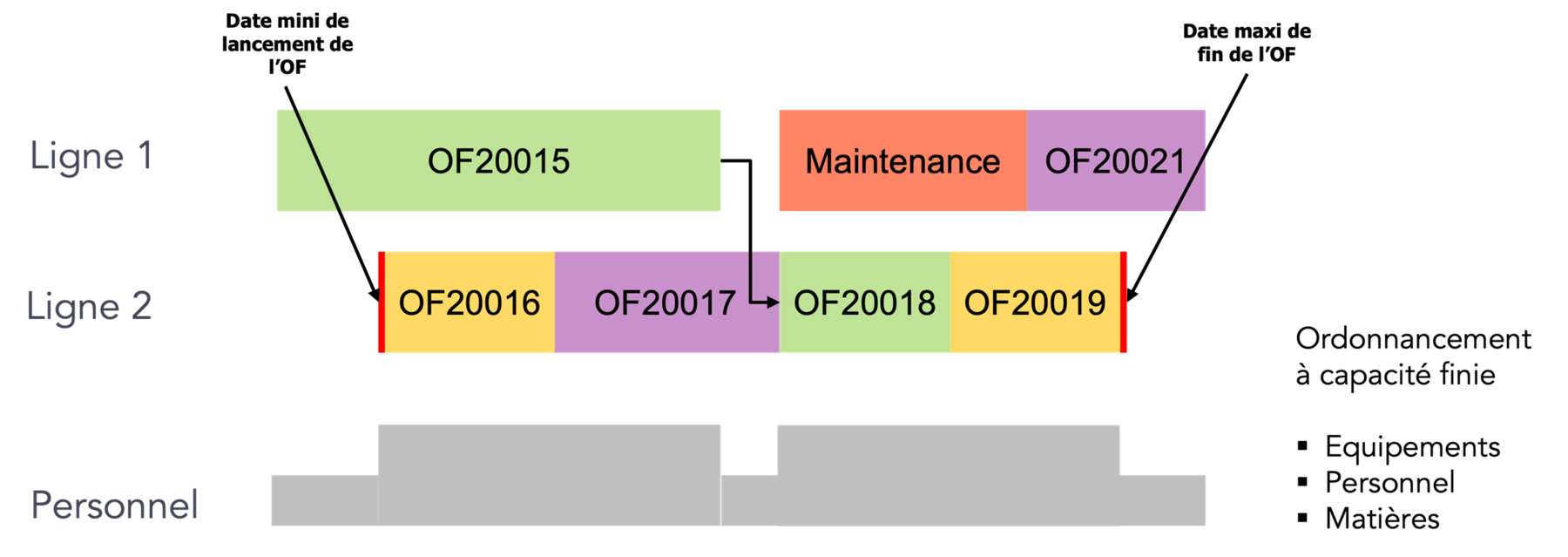
Par ses capacités temps-réel, le MES peut aller plus loin et informer la production de l’avancement des différents OF, avec une notion d’avance-retard pouvant être caractérisée par un indicateur : le taux d’adhérence au planning (% des OF faits dans les temps) pouvant être intégré dans une démarche d’amélioration continue.
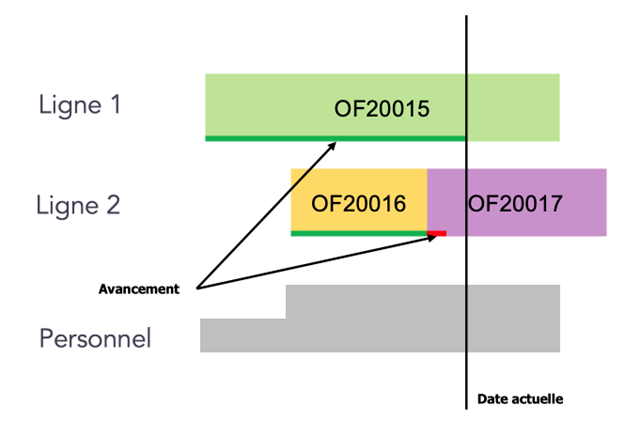
Forte valeur ajoutée du MES : anticipation
En s’appuyant sur le déroulement en temps réel constaté, un nouveau champ s’ouvre au MES : l’anticipation. En effet, le constat d’un OF en retard par rapport à son taux d’avancement prévu peut être lié à 3 causes non exclusives :
- L’OF a été lancé en retard
- L’OF a été pénalisé par des arrêts a priori exceptionnels
- L’OF s’exécute à une cadence inférieure à la cadence nominale
Suivant les causes identifiées du retard, on pourra anticiper la fin probable de l’OF et décaler le planning prévisionnel en conséquence. La figure 4 montre la différence d’anticipation de la fin d’un OF en retard suivant deux hypothèses : la première que les causes des pannes ou arrêts ayant amené le retard de l’OF ont été identifiées et ne vont plus se reproduire, la seconde que ces dernières ne sont pas maitrisées et qu’il faut donc les considérer jusqu’à la fin de l’OF.
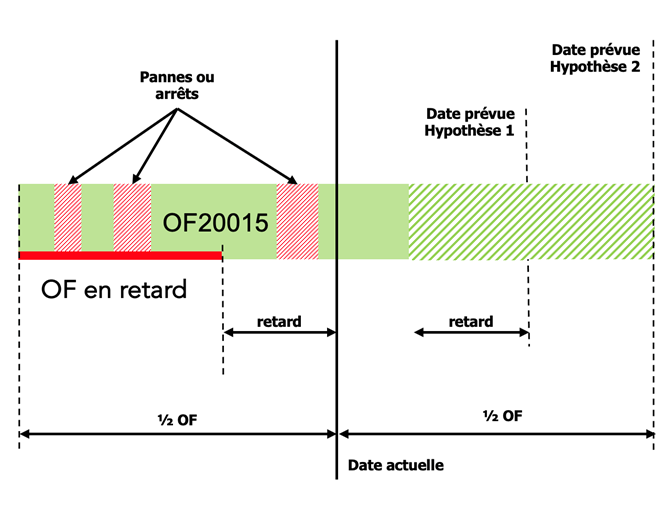
Suivant les capacités du logiciel de MES, le recalcul de la fin prévisionnelle de l’OF en retard pourra être reporté directement sur le planning (généralement après validation du planificateur) ainsi que les autres décalages en découlant sur les OF suivants utilisant les mêmes ressources. Le planificateur pourra le cas échéant réaménager la planification pour tenir compte de cette prévision avant qu’il ne soit trop tard pour répartir différemment les charges dans l’atelier.
En conclusion, nous voyons que le MES permet, par la mise en œuvre d’une planification temps-réel assistée, de compléter utilement la planification fournie par l’ERP, en donnant au responsable de la planification les clés pour connaissance détaillée, à la minute près, de l’avancement du plan de production, ainsi qu’une réactivité maximale face aux aléas et une anticipation suffisante des retards pouvant nécessiter un réaménagement du plan.