Le terme « traçabilité » recueille plus de 3 millions de résultats sur Google France, Pour fixer les idées, c’est environ un vingtième du nombre de résultats pour « logiciel ».
C’est une méthode très approximative, mais il est certain que la traçabilité occupe aujourd’hui une place centrale, et elle concerne principalement les industries.
Mais il est important pour commencer de bien poser de quelle traçabilité nous allons parler. En effet, le terme « traçabilité » est ce que l’on appelle un « mot valise ». On peut entendre plusieurs choses sous le terme de traçabilité.
Bien définir ce dont on parle va nous permette d’éviter par exemple, de penser que « la traçabilité est faite dans l’ERP » alors que ce qui est fait dans l’ERP, c’est le suivi des camions qui vont livrer les produits dans les magasins et la gestion des flux dans les entrepôts, alors que la traçabilité que l’on souhaiterait est celle des dysfonctionnements du procédé !
Dans le MES, la traçabilité qui nous intéresse est celle des fabrications. Et si dans le MES on parlera parfois de traçabilité de bout en bout, ce sera d’un bout à l’autre de l’usine. D’autres logiciels se chargeront d’étendre la traçabilité au-delà.
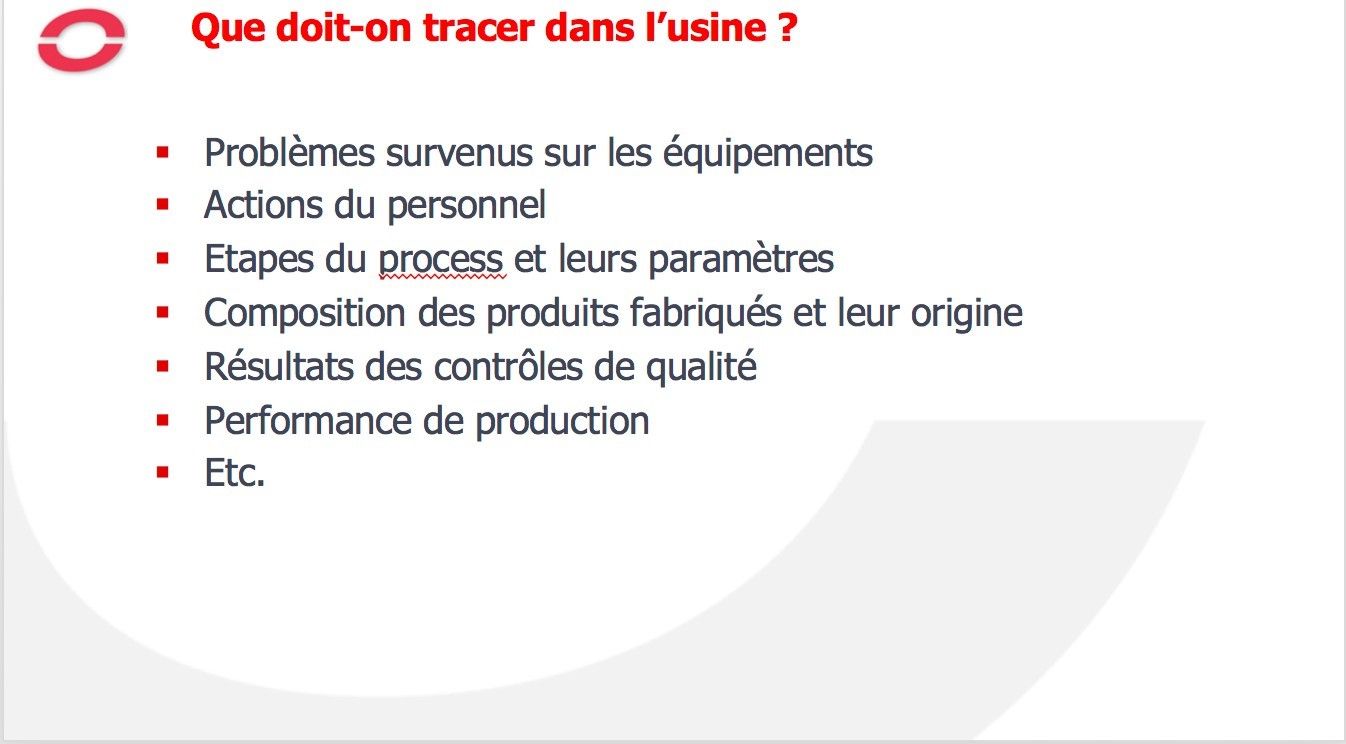
Mais même dans ce périmètre somme toute restreint, on peut vouloir tracer beaucoup de choses :
- Les problèmes survenus sur les équipements
- Les actions du personnel
- Les différentes étapes du process et leurs paramètres
- La composition des produits et leur généalogie (avec quels lots de matières premières ils ont été fabriqués)
- Le résultat des contrôles de qualité
- La performance de production
Bien sûr, l’industriel veut généralement tout tracer, mais si l’on veut parvenir à un résultat, il va falloir mettre un peu d’ordre.
Pour cela, nous allons reprendre les grands axes d’analyse de l’ISA-95, qui sont le personnel, les équipements, le procédé et les matières (ce dernier axe incluant également l’énergie).
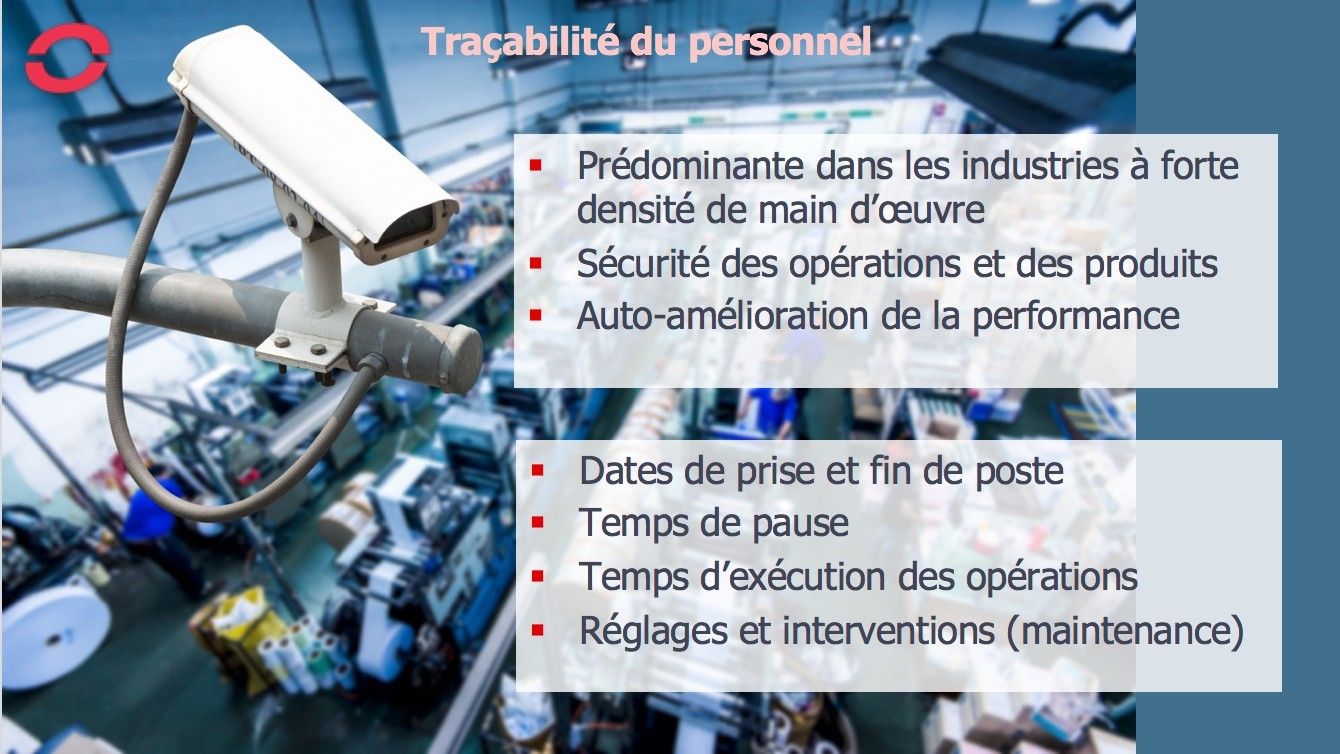
Commençons par la traçabilité du personnel.
Sans surprise, le souhait de tracer le personnel s’est manifesté de manière prédominante dans les industries de forte densité de main d’œuvre, avec l’objectif plus ou moins avoué de vérifier que les opérateurs ou les ouvriers respectaient les cadences et ne s’accordaient pas des temps de repos masqués hors des pauses prévues, et peut-être même de supprimer des postes.
Disons-le tout de suite, ce type d’objectif a contribué à donner une très mauvaise réputation de « flicage » aux premiers systèmes de MES, entrainant souvent le rejet brutal du système par les opérateurs et en définitive l’échec du projet. Nous verrons plus en détail dans une autre émission que l’adhésion des opérateurs est un facteur clé de réussite.
Un autre objectif majeur de la traçabilité du personnel est la sécurité, sécurité des opérations et sécurité des produits. Et la traçabilité est souvent dans ce cas une contrainte légale. S’assurer par exemple qu’un opérateur dispose des qualifications nécessaires pour effectuer une opération, ou qu’un responsable laboratoire a bien vérifié un dosage sont des exigences incontournables pour l’industrie pharmaceutique.
Enfin, bien informé, c’est à dire souvent informé en temps le plus réel possible des temps passés pour telle ou telle opération, l’opérateur pourra améliorer sa propre performance ou recevoir une formation complémentaire dans ce sens.
Les données que l’on souhaitera le plus souvent connaître sont les dates de prises et fin de postes, le décompte des temps de pause, mais aussi et surtout les temps d’exécution des différentes opérations, temps nécessaires pour les réglages et les interventions (maintenance).
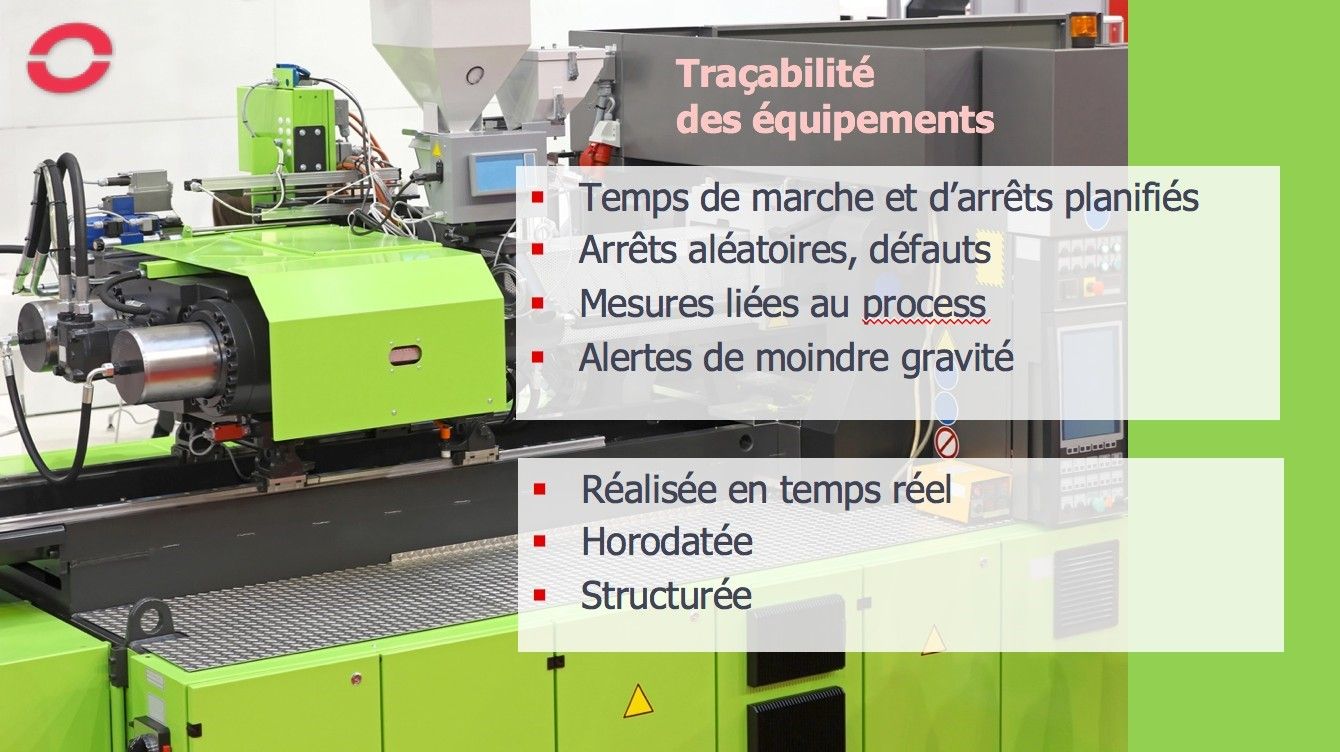
Venons-en à la traçabilité liée aux équipements…
La fabrication dans une usine ou un atelier n’est presque jamais uniquement constituée d’opérations manuelles. Il y a bien sûr des machines et la mise en place d’un suivi de production (le nom souvent employé pour un MES) nécessite l’obtention temps réel d’informations sur les équipements.
Dans les installations fortement automatisées, cela créé d’ailleurs une ambiguïté entre la couverture du logiciel de MES et celle des logiciels de supervision (ou SCADA) qui collectent aussi les informations au travers des automates. C’est un sujet que nous aborderons plus en détail dans le thème « MES et supervision ».
Que veut-on généralement tracer sur les équipements ?
- Les temps de marche et d’arrêts planifiés (fermetures, arrêts planifiés, maintenance)
- Les arrêts de défaut : disjonctions moteurs, niveaux hauts ou niveaux bas, dépassement de seuils, bourrage, …
- Les mesures effectuées sur ces équipements durant le process (températures, débits, pressions, …)
- Eventuellement des alertes de moindre gravité
Pour être utile et fiable, la traçabilité liée aux équipements doit vérifier certaines qualités :
- Réalisée en temps réel (et un véritable temps réel, plutôt qu’une saisie, est quasiment indispensable pour une traçabilité fiable)
- Elle doit bien sûr être horodatée
- Et elle doit être structurée (il doit être facile de relier l’information à l’équipement, à la section ou à l’atelier concerné)
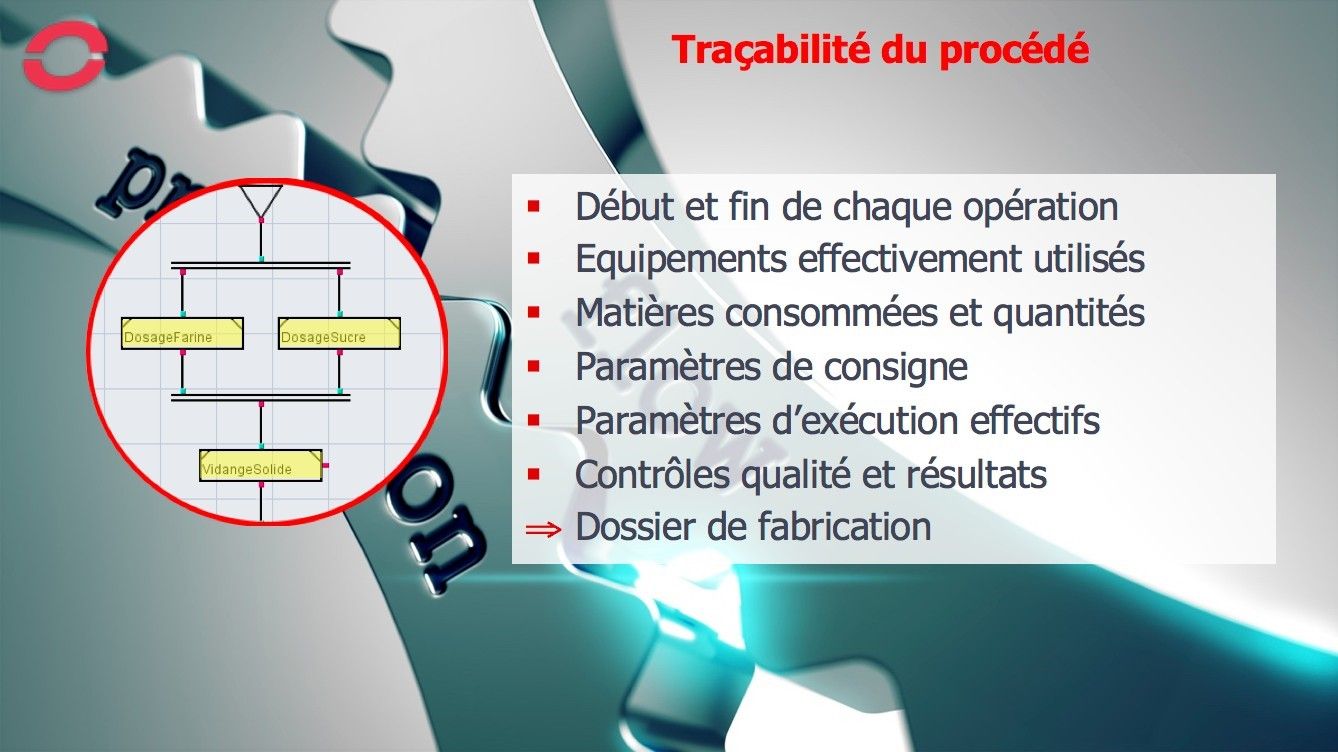
Voyons maintenant la traçabilité du procédé…
Un procédé est généralement constitué de différentes étapes, qui s’exécutent l’une après l’autre ou en parallèle. Suivant les industries et les installations, les procédés peuvent être plus ou moins complexes, et plusieurs fabrications peuvent s’exécuter simultanément en utilisant chacune à leur tour les mêmes équipements pour optimiser leur utilisation.
Que veut-on tracer sur le procédé et les opérations ?
- Les débuts et fins de chaque opération (début et fin dosage, début et fin de cuisson, d’assemblage, etc.), que ces opérations soient manuelles ou automatiques
- Les équipements effectivement utilisés : un procédé pharmaceutique dispose de plusieurs balances par exemple, laquelle a été utilisée pour le pesage (en cas de problème, on pourra vérifier si la balance a bien été étalonnée)
- Les matières utilisées et leurs quantités
- Les paramètres de consigne (température de consigne, débit de dosage, vitesse de coupe…etc.)
- Les paramètres d’exécution mesurés (quantités réelles, résultats des contrôles,
…etc.)
- Les contrôles de qualité et leurs résultats : ces contrôles de qualités peuvent être des contrôles en ligne, analogues aux étapes du procédé, ou des contrôles hors ligne, d’une organisation différente
L’ensemble de ces informations est souvent rassemblé dans un dossier de fabrication. Pour les fabrications pat lots, on parle aussi de dossier de lot.
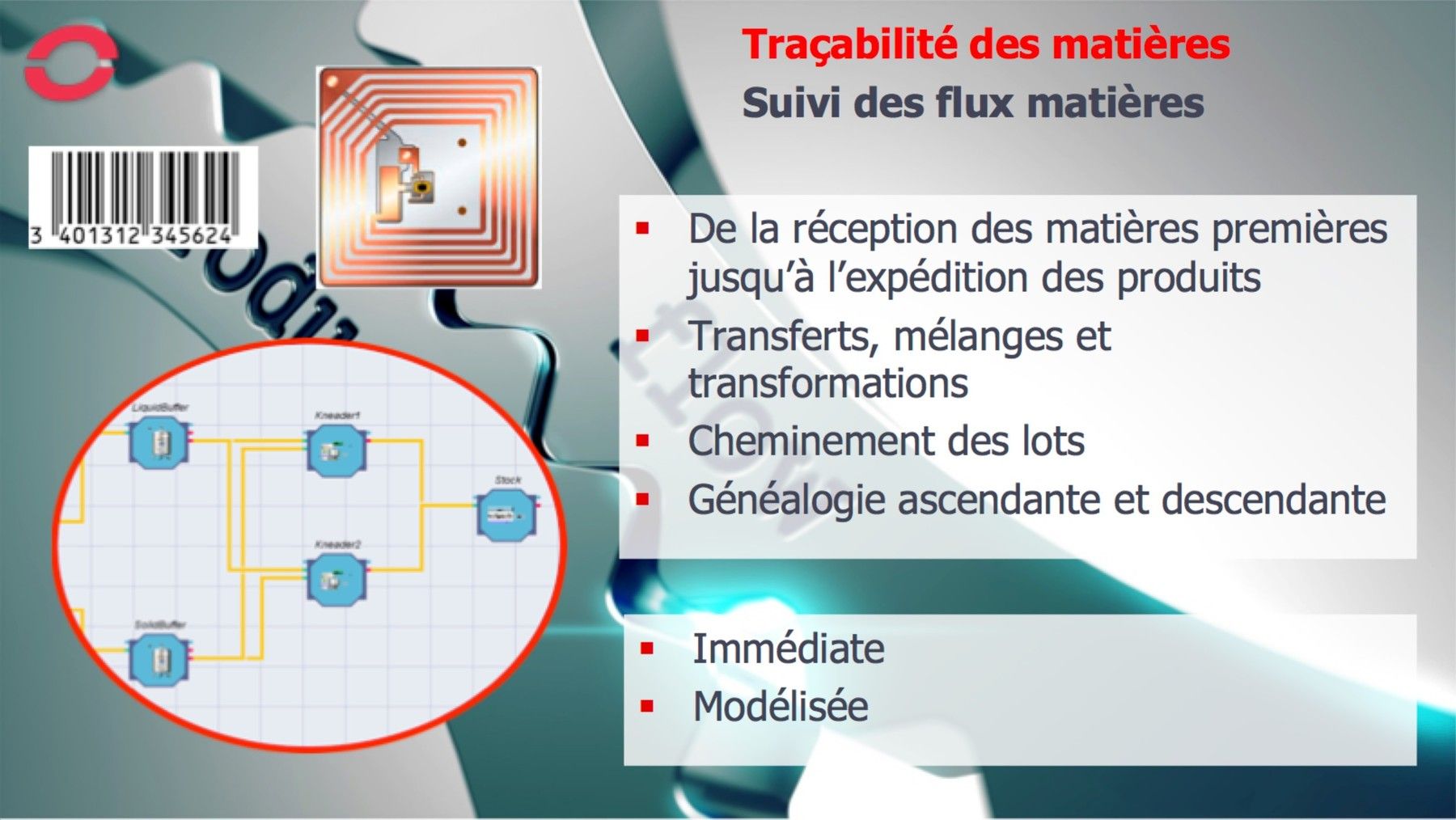
Enfin terminons par la traçabilité des matières – on parle d’ailleurs souvent de suivi des flux matières – ce qui est peut-être plus explicite.
Le suivi des flux matières s’étend de la réception des matières premières jusqu’à l’expédition des produits.
Lors de la fabrication, les lots de matières ou de composants sont amenés à traverser plusieurs équipements, avec différents chemins physiques possibles. Lors de traversée d’un équipement, un lot de matière ou de composants pourra rester inchangé. Il s’agit alors d’un simple déplacement.
Mais il pourra aussi être empilé ou dépilé avec d’autres lots, ou transformé.
On utilise généralement des dispositifs tels que les codes à barres, ou des puces RFID pour identifier les produits en entrée et en sortie des fabrications. Ces dispositifs peuvent être appliqués sur des produits solides, des cartons ou des containers de toute sorte. Pour ses produits liquides ou pulvérulents, ils peuvent être utilisés au niveau des lots seulement. Un lot pourra d’ailleurs être mélangé à d’autres lots de matière identique ou de matières différentes, pour former un produit intermédiaire, et les produits intermédiaires peuvent être identifiés ou non.
Pour garantir la composition et la qualité de ses produits, les industriels doivent tracer ces informations et être capables de retracer rapidement le cheminement d’un produit fini en cas de problème (par exemple un équipement défectueux identifié dans la chaine de production ou contaminé). En mettant en place des algorithmes appropriés, il est également possible à partir d’un lot de produit fini, d’identifier les lots de matières premières ou de composants (et donc l’origine) qui ont servi à le fabriquer, ce que l’on appelle la généalogie ascendante. Inversement, par un mécanisme similaire, on peut identifier à partir d’un mot de matière première ou de composants les lots de produits finis qui l’ont utilisé, ce que l’on appelle la généalogie descendante.
Certains logiciels de MES disposent d’algorithmes prédéfinis qui permettent de modéliser le comportement des équipements pour l’ensemble de l’installation, et donc d’obtenir automatiquement la généalogie ascendante ou descendante de l’installation. L’adéquation de ces mécanismes au procédé de l’industriel dépendra bien sûr des cas de figure (empilement, dépilement, extraction, mélange, transformation, etc.) devant être pris en compte.
Que veut-on tracer sur les flux matières ?
- Les flux matières commencent avec la réception des matières premières, qu’il faut identifier en nature, en quantité et en contenant de stockage
- On souhaite évidemment tracer tous les transferts de matières, ainsi que les mélanges et les transformations
- On souhaite également tracer les mouvements des stocks d’atelier
- Ce qui permettra d’obtenir la généalogie ascendante et descendante des produits
Quelles sont les exigences concernant la traçabilité matières ?
- Une traçabilité matières sera souvent utilisée pour prévenir une situation de crise. Pour être réellement utile, elle doit donc être immédiate. Certaines industries, comme les industries alimentaires, ont des obligations légales à cet égard.
- Enfin dans beaucoup d’installations, les combinaisons possibles sont trop nombreuses pour être codées au cas par cas. Il faut donc pouvoir modéliser l’installation et que cette modélisation soit à la base du suivi des flux matières
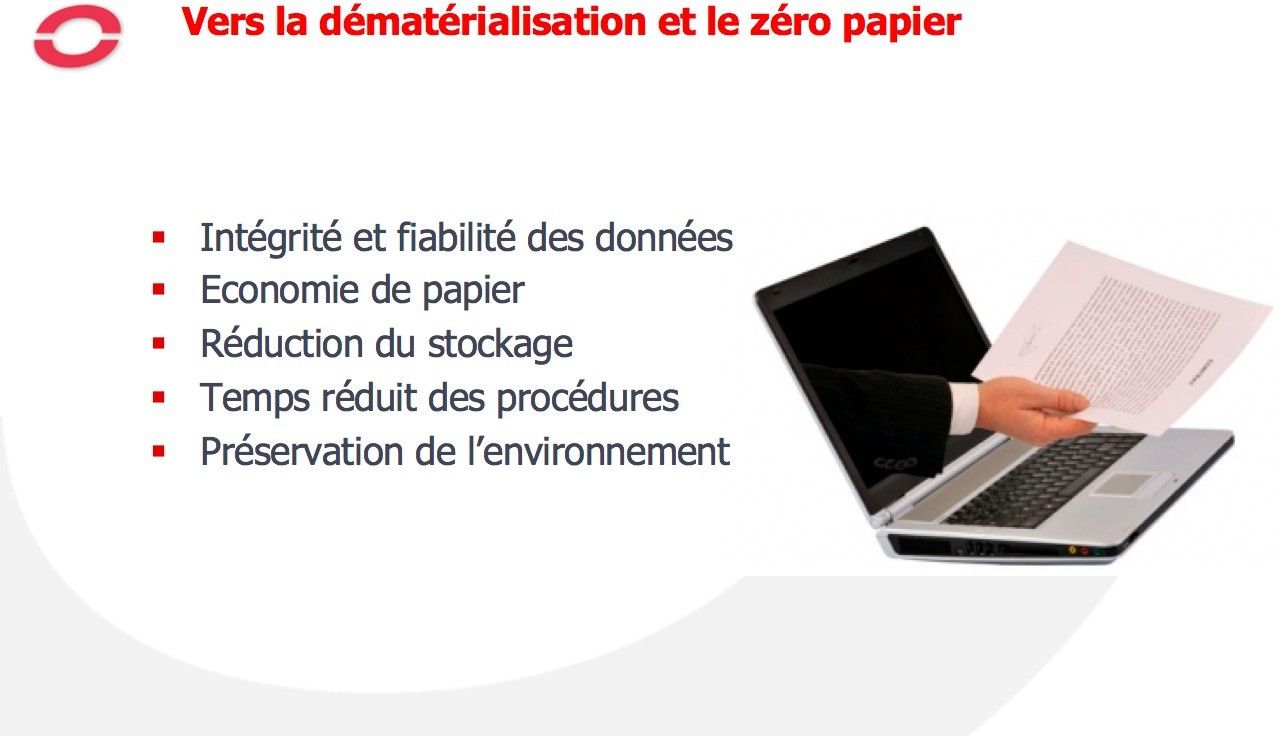
La traçabilité informatique s’inscrit dans les démarches de dématérialisation et de « zéro papier ». Elle en partage donc les avantages :
- L’informatique permet de garantir l’intégrité des données, c’est à dire que ces données ne sont pas altérées de manière accidentelle ou volontaire. A noter que cela suppose souvent la mise en place de mécanisme dédiés (contrôles d’intégrité, redondance).
- De manière évidente, la dématérialisation permet une réduction des coûts : coûts de papier bien sûr, mais également coûts d’impression (qui sont souvent plus importants que le coût du papier lui-même) et coûts de stockage des
- La dématérialisation permet également de réduire les temps d’exécution des procédures, qu’il s’agisse de procédures de recherche, comme celles que l’on a évoquées pour la généalogie, ou de procédures administratives mettant en jeu le transfert de documents. Les documents vont pouvoir être échangés simplement par email ou par des procédures électroniques dédiées. Sur le plan administratif, il faut tout de même noter que les documents devront généralement être fournis sous un format bien précis, et donc il faudra souvent effectuer un traitement à partir des données internes pour délivrer les documents administratifs exigés.
Enfin dernier point et non des moindres, la dématérialisation des documents permet de préserver l’environnement, en évitant d’une part la production de grandes quantités de papier par les papeteries qui sont des industries très polluantes, et d’autre part en supprimant la nécessité de traiter au bout du compte les déchets à l’expiration des durées de conservation des documents.
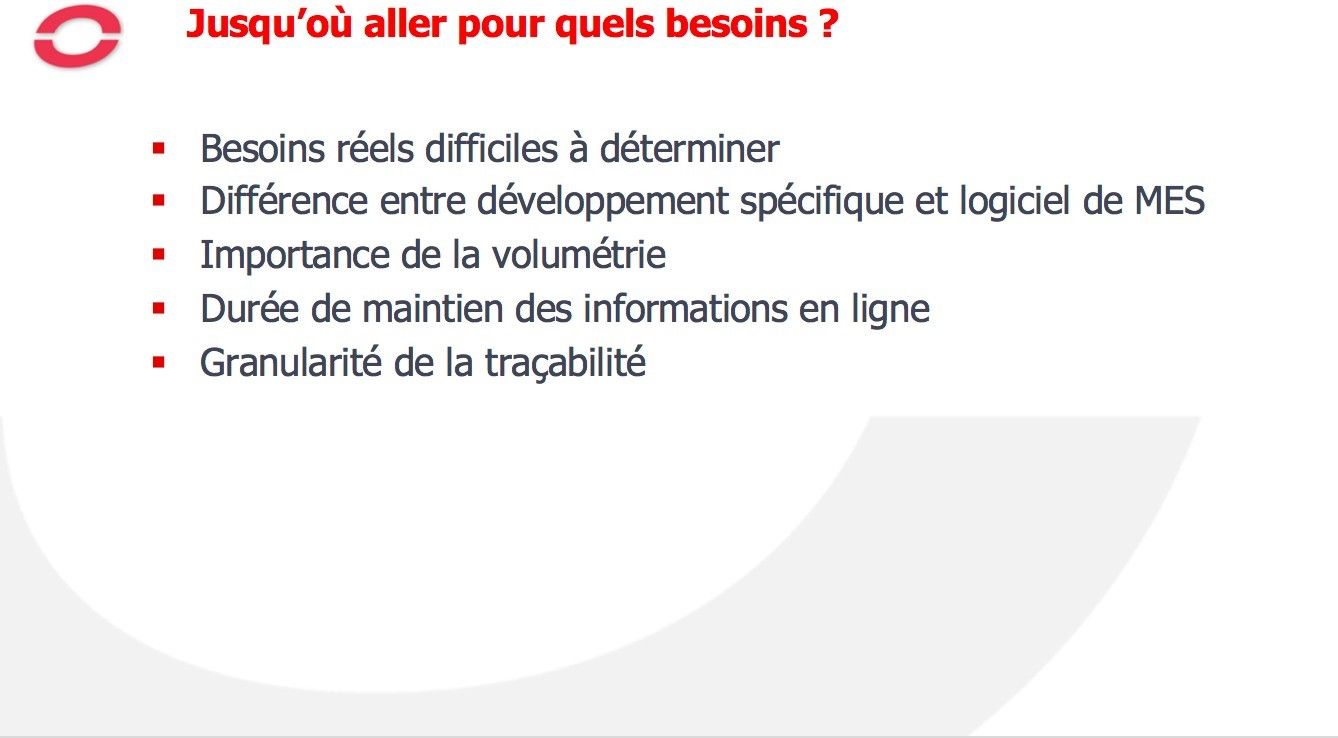
Revenons au contenu de notre traçabilité informatique. Même si nous nous sommes limités à la traçabilité des fabrications uniquement, on voit bien que cette fonction du MES est extrêmement riche, et induit différentes sous-fonctions qui se complètent. Alors on peut être tenté de dire : a-t-on vraiment besoin de tout cela ? Et la mise en place de ces différents aspects de la traçabilité ne va-t-elle pas induire de lourdes charges de développement sans retour de profitabilité. Choisissons de tracer uniquement les informations dont nous avons réellement besoin, ou qui nous sont légalement imposées ! En fait, la réponse n’est pas aussi évidente qu’il y paraît.
D’une part, il est assez difficile de déterminer a priori les informations dont on va avoir besoin. Supposons que l’on fabrique des biscuits. Assez naturellement, on jugera nécessaire de tracer les ingrédients, les quantités de matières premières consommées et les résultats des contrôles qualité, mais peut-être pas immédiatement l’ensemble des paramètres du procédé. Pourtant, si le contrôle qualité est défectueux, et que par exemple les biscuits sont trop cuits, un opérateur ne manquera pas de faire remarquer que l’on aurait dû tracer la consigne de température pour la cuisson !
D’autre part, il faut noter qu’il y a une grande différence de charge de développement suivant la façon dont on réalise la traçabilité. S’il s’agit d’un développement spécifique, toute information supplémentaire tracée se traduit par un coût de développement et de test (ce dernier point n’est pas négligeable car à quoi sert une traçabilité si elle n’est pas fiable).
Si la fonction de traçabilité souhaitée est réalisée par un logiciel de MES, la trace d’un paramètre supplémentaire n’entraine pas d’autre coût que celui de la collecte du paramètre. S’il s’agit d’un paramètre du process, il est probable qu’il se trouve déjà dans le système et il n’y a pas de coût additionnel. Ce n’est donc pas une raison pour se priver d’informations importantes.
Si les fonctions de traçabilité sont assurées par un logiciel de MES, le point qui sera à surveiller sera en fait la volumétrie des données. Si les données sont acquises à un rythme rapide (par exemple pour de hautes cadences de fabrication), alors les facteurs multiplicatifs peuvent être très importants, et entrainer les volumes de stockage prohibitifs. La volumétrie proprement dite est de moins en moins un problème, mais peut déboucher sur une réactivité médiocre du système, en particulier si des mécanismes de compression/décompression doivent être utilisés.
Pour conserver des volumétries raisonnables et une bonne réactivité de l’application, il faudra se poser deux questions :
- Sur quelle durée dois-je maintenir les données de traçabilité « en ligne » (un archivage longue durée pourra en effet être mis en place pour compléter, cet archivage longue durée pourra d’ailleurs être utilisé pour la Manufacturing Intelligence – On se rapproche des technologies « big data ») ?
- Quelle est la granularité de traçabilité réellement nécessaire : par exemple, ai-je besoin de connaître les consignes et valeurs effectives au niveau de chaque opération élémentaire, ou uniquement pour des blocs d’exécution complets. Ou dois-je connaître précisément le cheminement des matières au travers de chaque équipement, ou uniquement les matières qui entrent et qui sortent de chaque unité de production ?
Je vous propose de résumer ce que nous avons vu aujourd’hui sur le thème de la traçabilité.
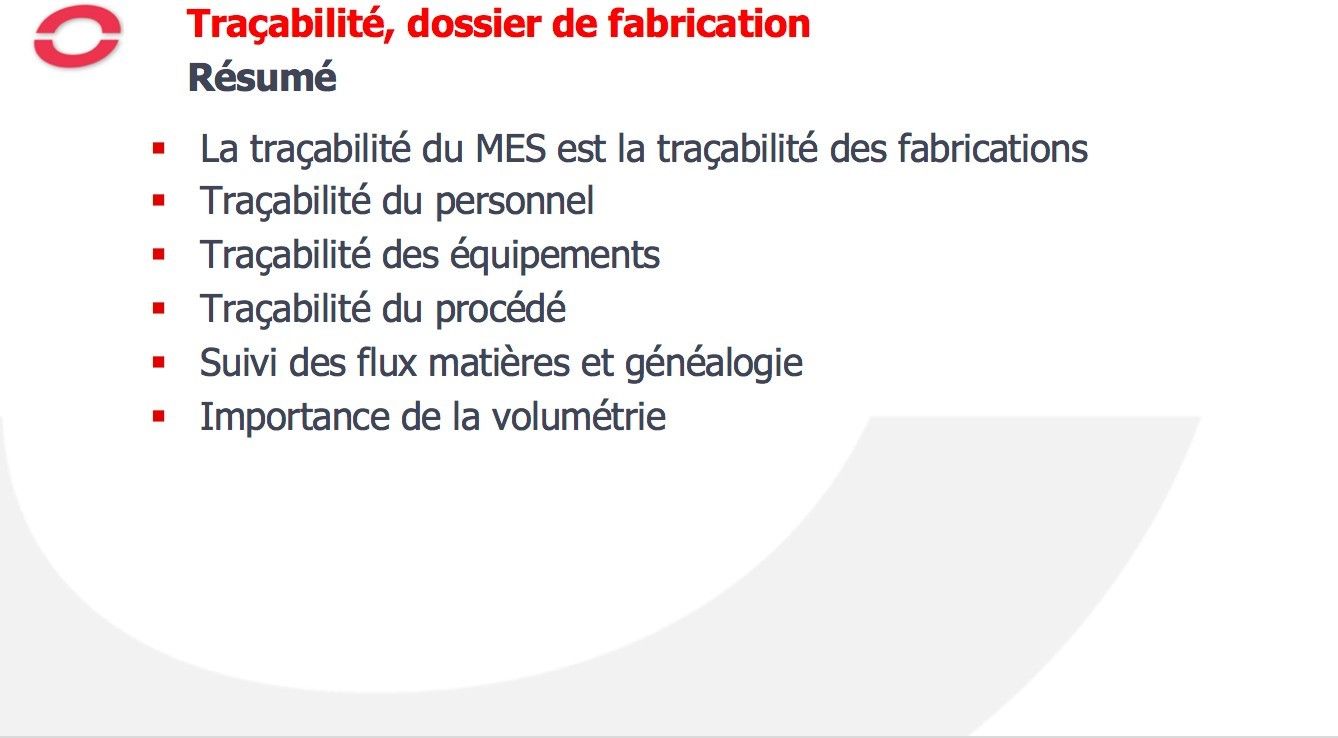
Tout d’abord, nous avons vu que la traçabilité du MES est en fait la traçabilité des fabrications, et que son périmètre est l’usine ou l’atelier.
Nous avons vu la traçabilité du personnel, ses limites et sa bonne utilisation
La traçabilité des équipements qui n’est pas sans évoquer certaines fonctions de supervision La traçabilité du procédé
Le suivi des flux matières et la généalogie
Puis nous avons vu les points qu’il fallait réellement considérer pour maîtriser la traçabilité, et en particulier le lien entre volumétrie et réactivité.