Le ROI - de l’anglais Return On Investment - d’un projet, est le ratio entre les gains apportés par le projet et son coût total, incluant l’investissement initial et les coûts récurrents. On l’exprime généralement en années ou fractions d’années nécessaires pour que les gains équilibrent l’investissement total réalisé, les années suivantes amenant un gain net.
Pour un projet MES, le calcul du coût total ne pose généralement pas de problème, même s’il faut évidemment bien prendre en compte les coûts de maintenance, et le coût des ressources complémentaires qui peuvent être nécessaires pour l’utilisation du système.
On trouvera en particulier dans le livre blanc « Valorisation d’un projet MES », diffusé gracieusement par le Club MES, des méthodes complètes pour le calcul des coûts.
Plus délicat est le calcul des gains apportés par un système MES, et c’est par ce sujet que nous allons commencer cette émission.
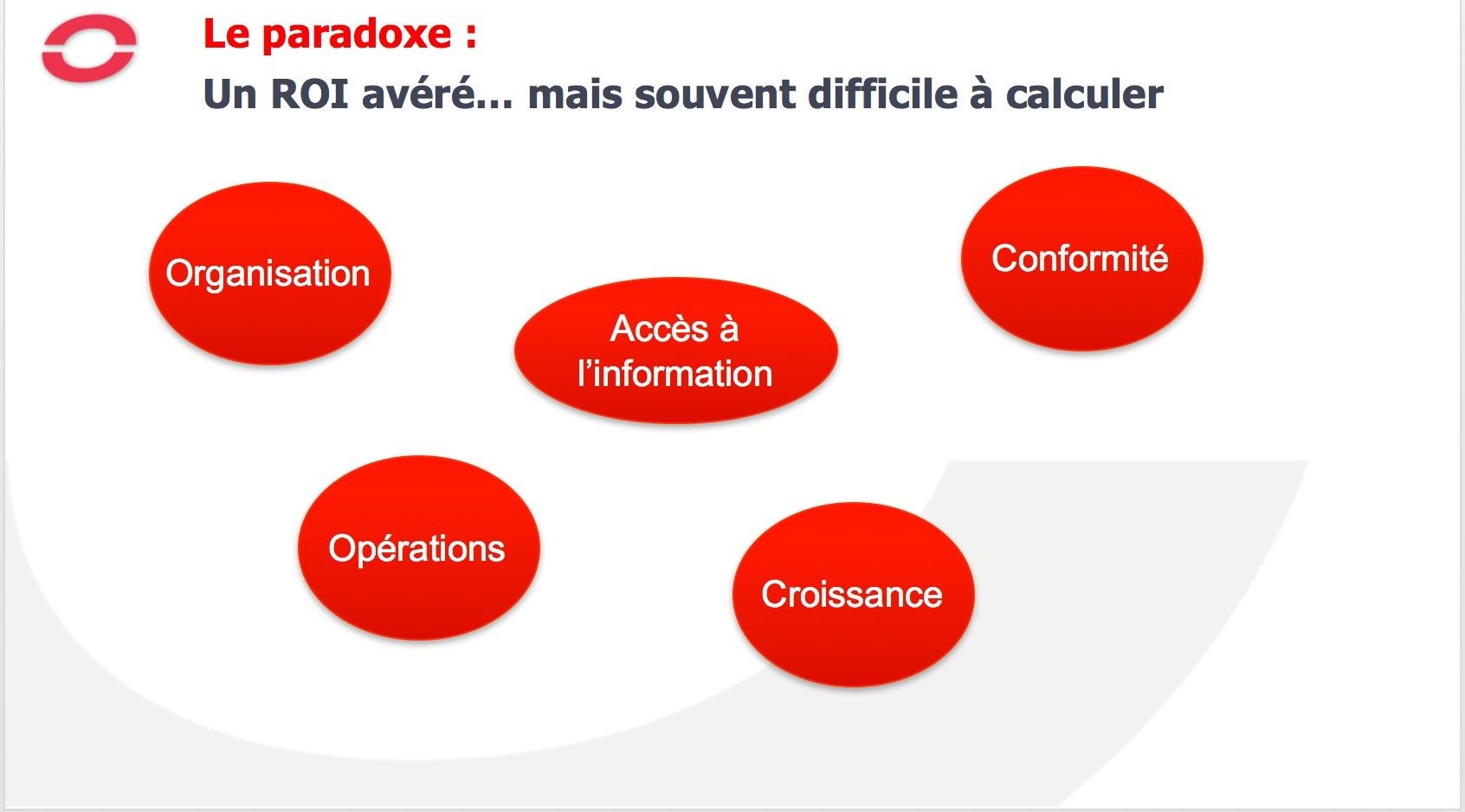
On demande en effet presque systématiquement, en amont du lancement d’un projet MES, quels sont les gains que ce projet va apporter. Et alors, on est confronté au paradoxe que si ces gains sont avérés, ils sont le plus souvent difficile à calculer.
En effet, les gains potentiels d’un projet MES sont nombreux et ont été recensés dès le début de l’activité MES par le MESA :
- Organisation : un système MES contribue à la formalisation et à la standardisation des processus opératoires, et par là-même à la rationalisation de la production. Grâce à ses fonctionnalités d’ordonnancement et par l’intégration de méthodes du lean manufacturing, il permet une optimisation des flux. En objectivant les problèmes rencontrés, il contribue également à la motivation du
- Croissance : un système MES soutient efficacement la croissance de l’entreprise en augmentant ses capacités de production par une utilisation plus efficace des équipements. Il renforce l’agilité de l’entreprise par la flexibilité des procédés et du personnel, la réactivité en cas d’aléa de production.
- Accès à l’information : fournir la bonne information, à la bonne personne, au bon moment, est un enjeu actuel pour la plupart des entreprises auquel répond parfaitement le MES dans le domaine de la production, qu’il s’agisse de documents de traçabilité, de dossiers de fabrication, de rapports d’activités, etc.
- Opérations : (gain au niveau des opérations). Le système MES peut permettre des réductions de personnel, mais aussi souvent la réaffectation du personnel à des tâches à plus forte valeur ajoutée. Il peut amener la réduction des heures d’ouvertures (par exemple le passage de 3/8 en 2/8) et donc une réduction des coûts variables associés, qu’il s’agisse de charges de personnel ou de charges comme le chauffage, l’éclairage et les autres énergies. Par l’analyse de la performance, il amène une réduction des défauts, la réduction des consommations de matières premières et une augmentation des marges. Par la réduction du temps machine, il amènera également une réduction de la consommation énergétique
- Conformité à des normes contraignantes : qu’elles soient de l’ordre de la loi ou simplement des exigences de la clientèle, les normes à respecter pour la fabrication sont de plus en plus fortes. Si elles sont subies sans être intégrées au système de production, elles se traduisent par un surcoût humain, des perturbations de la production et un facteur de risque accru pour la pérennité de l’entreprise. Le système MES permet d’intégrer ces contraintes incontournables et le plus souvent d’en tirer bénéfice pour l’optimisation de la production.
- Autres sources de gains : d’autres sources gains sont plutôt liées à la réalisation du projet et se traduiront en fait par une réduction des coûts. Elles pourront concerner l’infrastructure comme les technologies de virtualisation, ou la méthodologie de réalisation pour les projets multi-site, avec en particulier la mise en œuvre d’un « core model », sur laquelle nous reviendrons juste après.
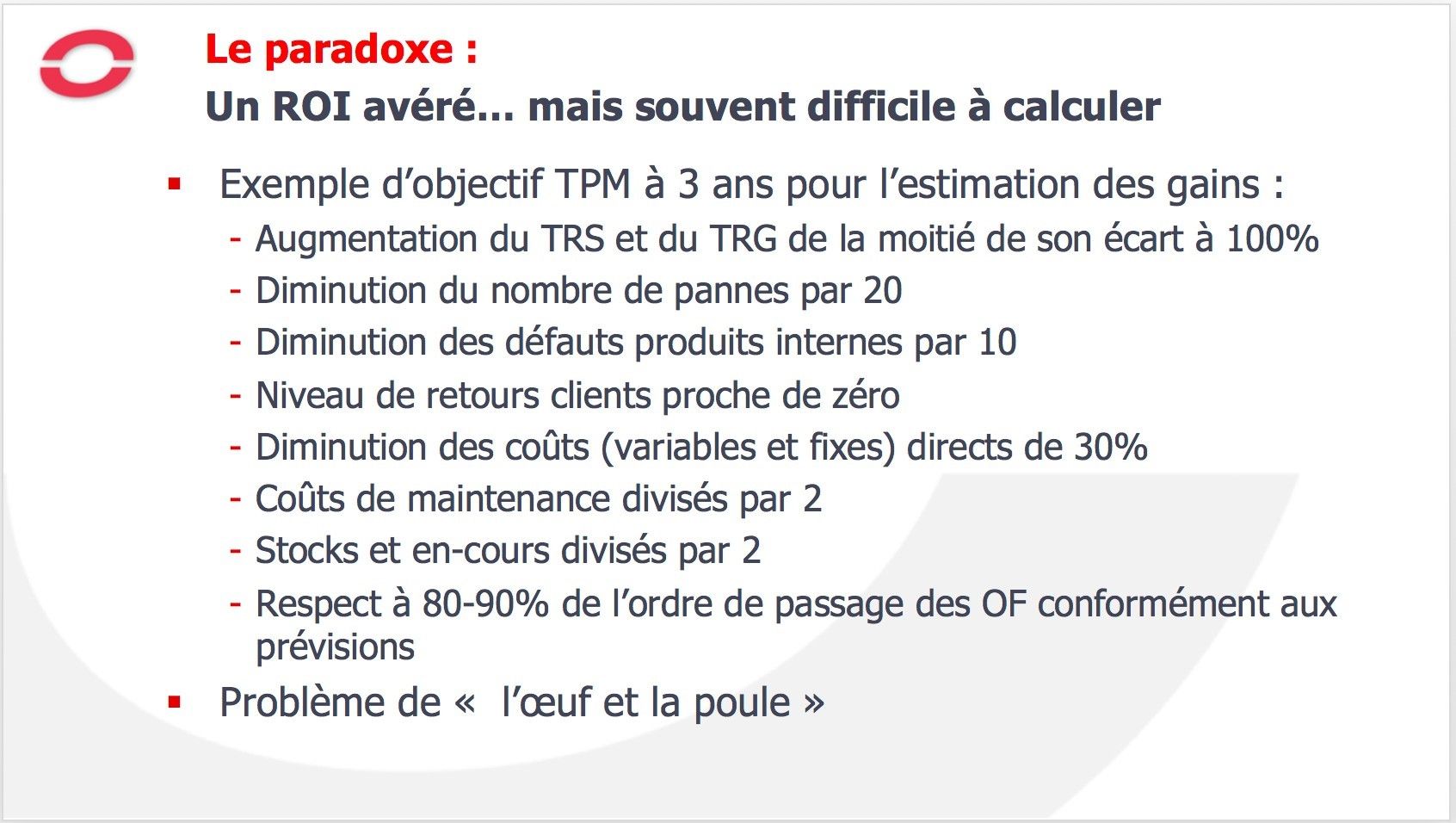
Tous ces gains sont bien réels, mais seuls une partie d’entre eux, et pas forcément les plus importants, peuvent être estimés avec une précision acceptable. A titre d’exemple, les démarches TPM associées aux indicateurs de type TRS ont un objectif à 3 ans de :
- Augmentation du TRS et du TRG de la moitié de son écart résiduel à 100%
- Diminution du nombre de pannes par 20
- Diminution des défauts produits internes par 10
- Niveau de retours clients proche de zéro
- Diminution des coûts (variables et fixes) directs de 30%
- Coûts de maintenance divisés par 2
- Stocks et en-cours divisés par 2
- Respect à 80-90% de l’ordre de passage des OF conformément aux prévisions
Mais pour beaucoup de sources de gains, on sera confronté à un problème de l’œuf et de la poule : pour estimer le gain, il faudrait disposer d’un système de mesure fiable (temps passés dans les opérations, temps d’arrêt, matières consommées, etc.) et c’est justement le MES qui est ce système de mesure !
Une fois le système mis en place, on peut effectivement mesurer au fil de temps les gains réalisés. Ce calcul n’est pas toujours fait et surtout, pour diverses raisons, les industriels souhaitent rarement communiquer dessus.
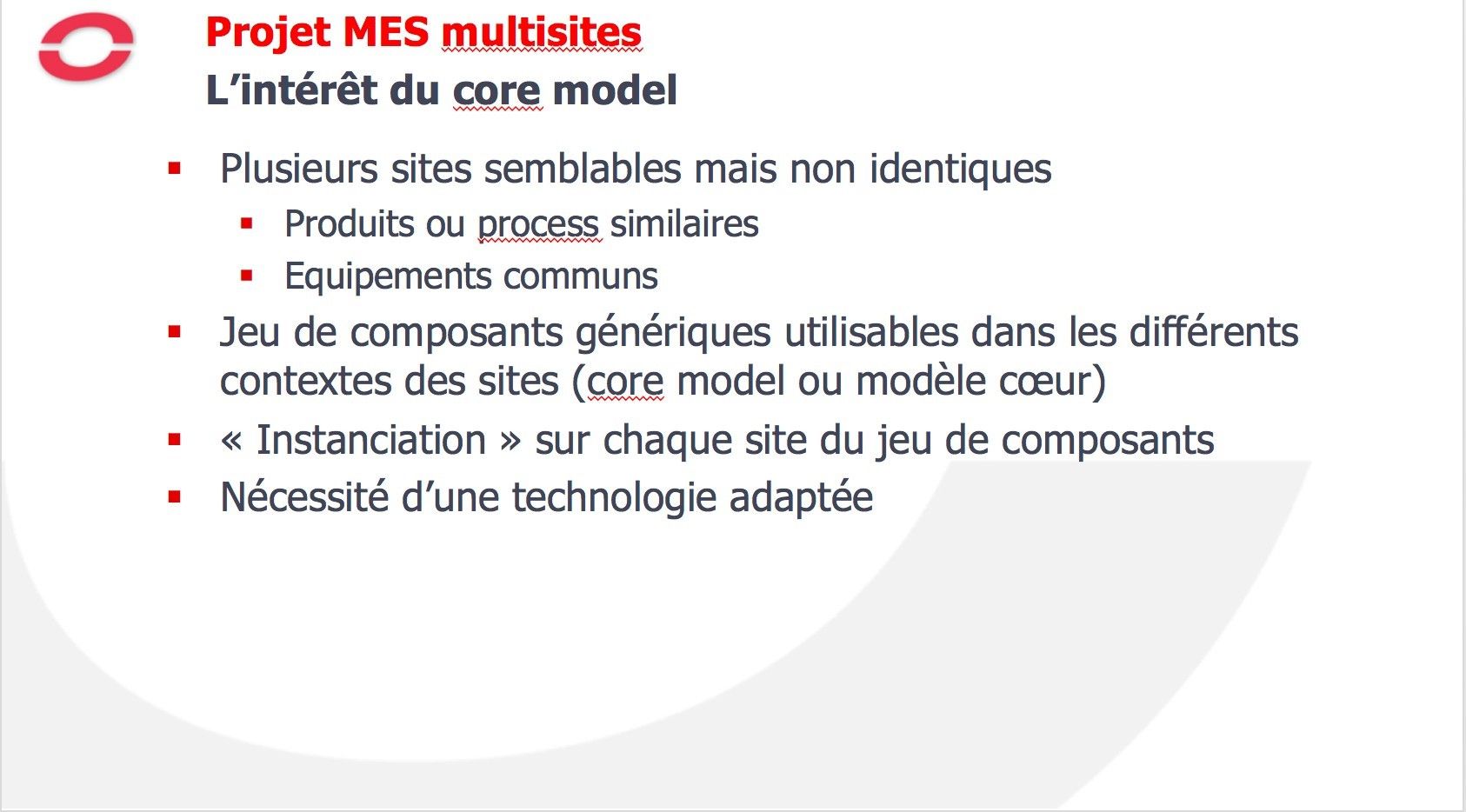
De nombreux clients industriels disposent de plusieurs sites. Ces sites sont rarement identiques, mais présentent des similitudes liées au métier de l’industriel :
- Ils vont fabriquer des produits similaires, ou les produits sont différents mais l’industriel a utilisé son savoir-faire en termes de process pour les différentes productions. Par exemple des viennoiseries et des pizzas présentent de grandes similitudes de process.
- On va retrouver le même type d’équipement ou des équipements similaires sur plusieurs sites.
Le principe du « core model » ou « modèle cœur » est de réaliser un jeu de composants génériques utilisables dans les différents contextes des sites.
La réalisation va donc se faire en deux étapes : la réalisation du « core model » et son utilisation (on parle d’instanciation) sur chacun des sites.
On voit bien que l’on parle de composants, ou d’objets. Même si sur le papier on peut toujours suivre cette approche, elle ne pourra être implémentée efficacement qu’en disposant dans le logiciel MES d’une technologie adaptée.
Pour voir le bénéfice d’une telle approche, nous allons comparer la méthode traditionnelle de développement et la méthode core model pour la mise en œuvre d’un projet MES.
Chaque projet comporte des coûts fixes (le matériel à acquérir en particulier, en rouge) et des coûts de développement (en jaune).
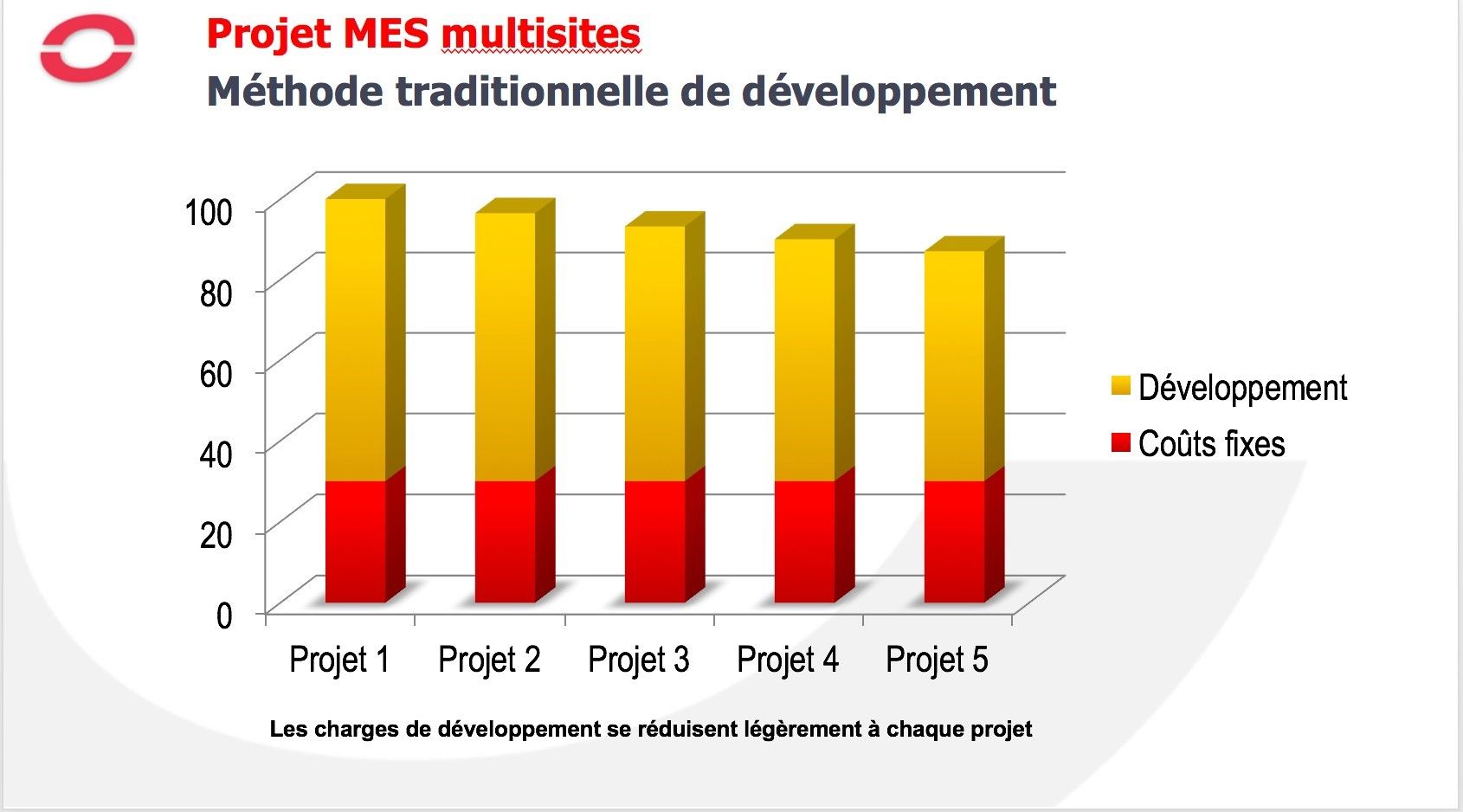
Avec une méthode traditionnelle de développement, compte tenu des similitudes entre les sites, les charges de développement se réduisent légèrement à chaque projet du fait d’une meilleure maitrise des situations rencontrées, mais les gains restent très modérés.
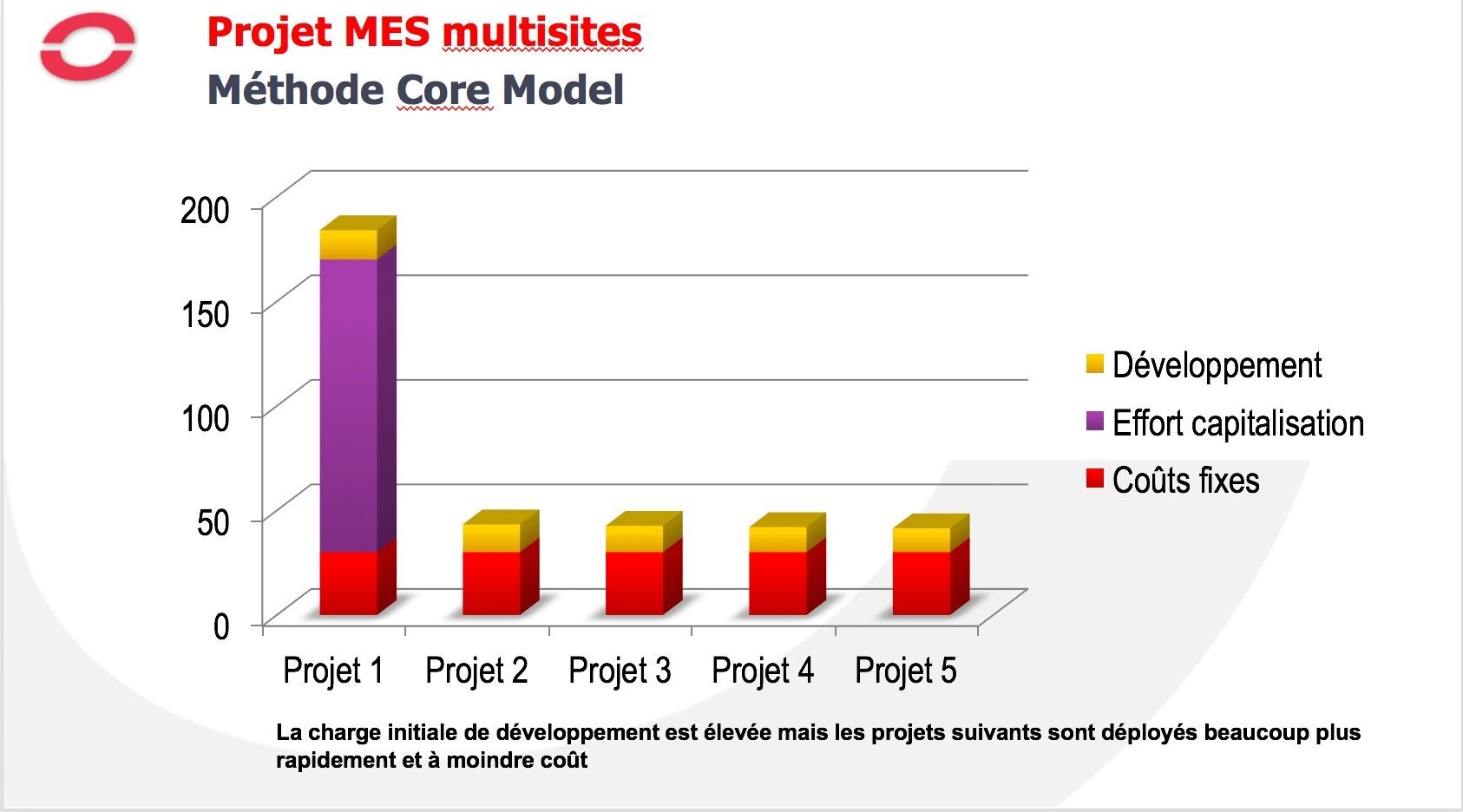
Avec une méthode core model et une technologie logicielle adaptée, un effort initial est nécessaire pour la réalisation du core model, qui nécessitera une analyse générique des contextes de l’ensemble des sites, donc plus complexe. On retrouve cet effort de capitalisation ici associé au premier projet.
Mais la phase d’instanciation sur chacun des sites est beaucoup plus courte. Si de plus la technologie permet de garantir la reproductibilité des modèles utilisés, les phases de test sont également grandement réduites (les fonctions internes aux modèles n’ont pas besoin d’être re-testées).
La charge de développement initiale est évidemment plus élevée mais les projets suivants sont déployés beaucoup plus rapidement et à moindre coût.
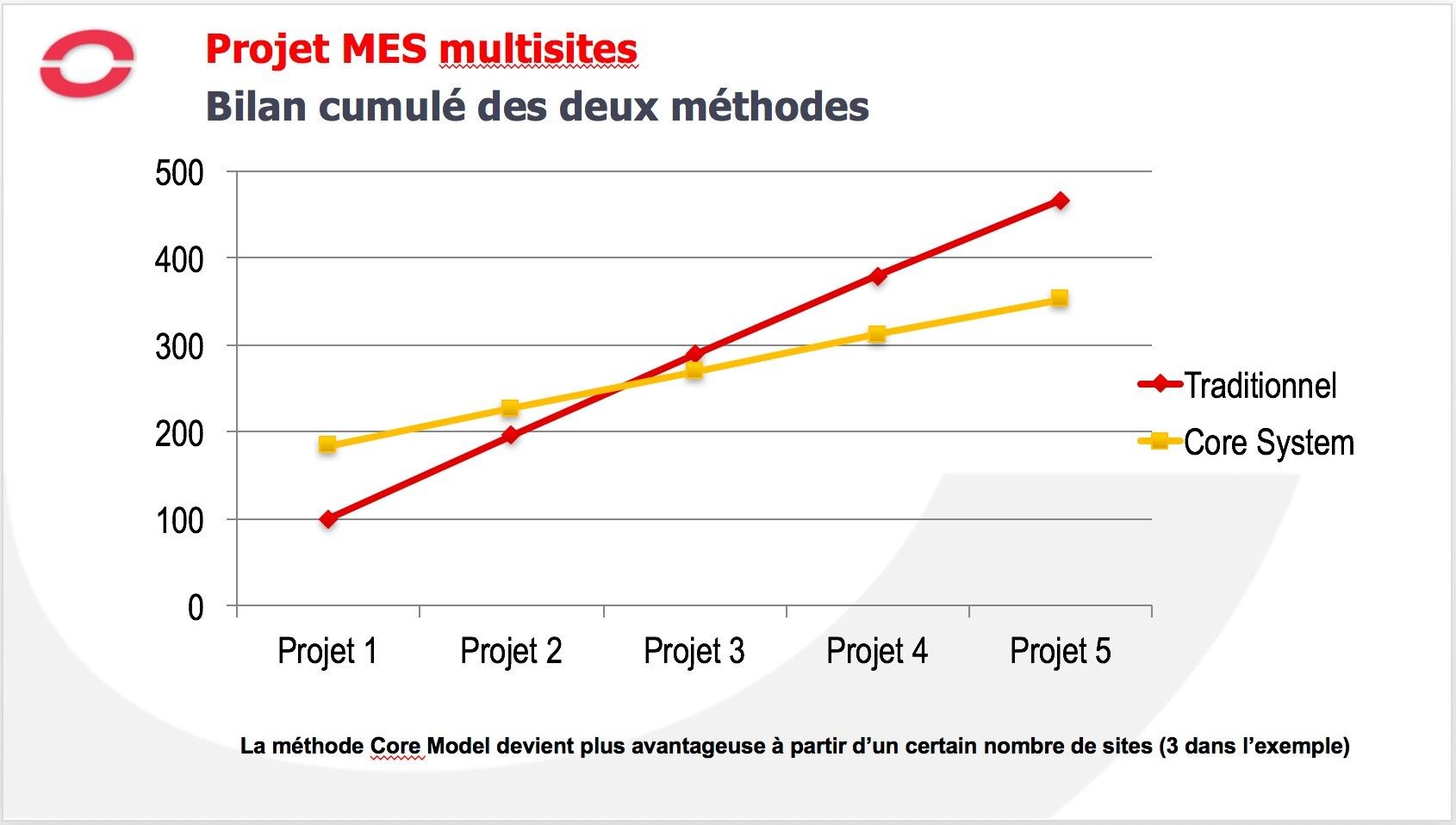
Le bilan entre les deux méthodes est clairement à l’avantage de la méthode Core Model à partir d’un certain nombre de sites, généralement à partir de 3.
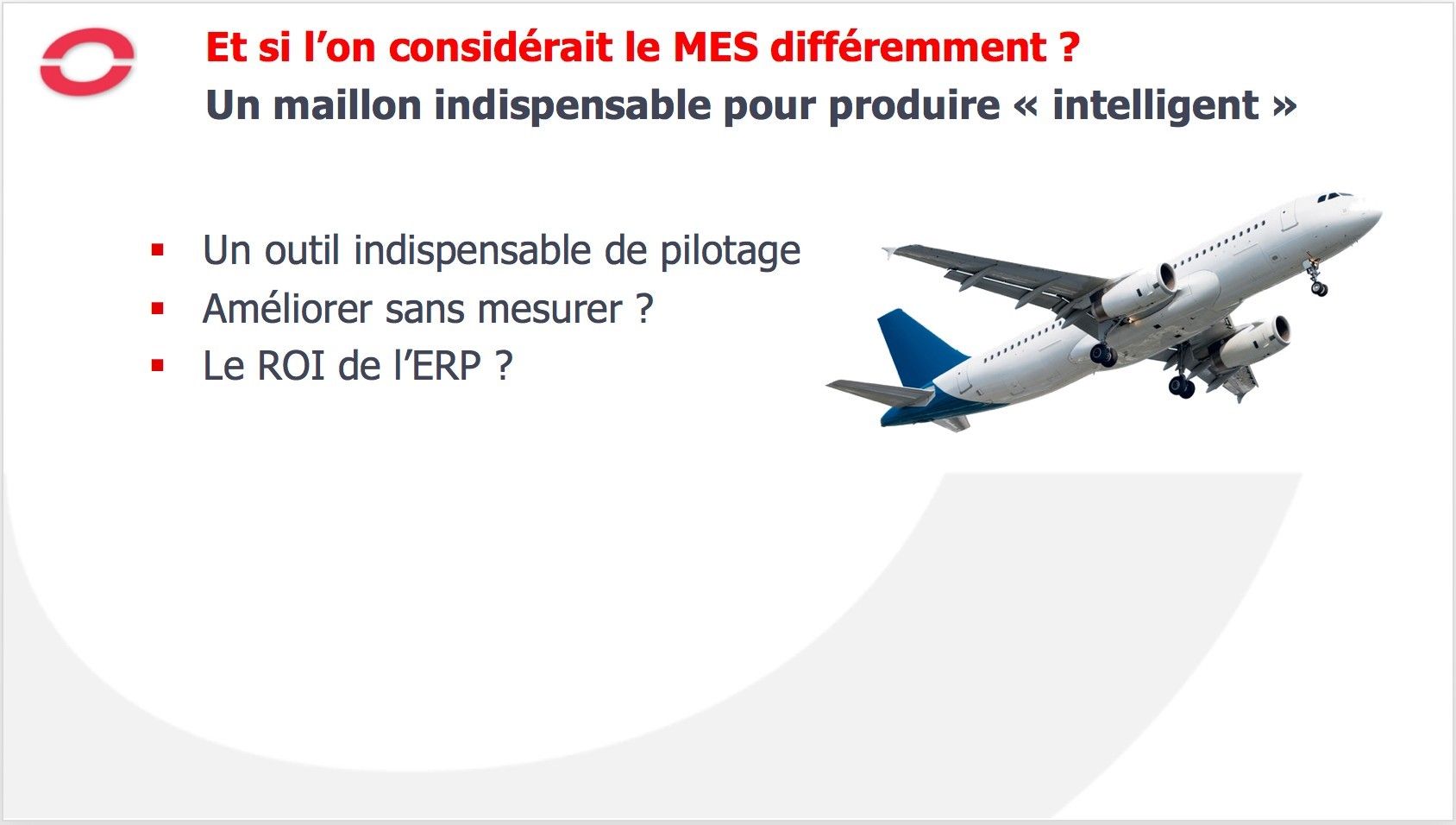
Et si l’on considérait le MES différemment ?
Si l’on a l’occasion d’entrer dans le cockpit d’un avion de ligne, on est frappé par le nombre d’indicateurs de pilotage. Il ne viendrait à l’idée de personne de demander au pilote d’oublier tous ces indicateurs et de piloter l’avion les yeux bandés. Un outil de production est-il si simple que l’on puisse procéder différemment ? Non ! Eh bien c’est précisément ce qu’est un MES, un outil indispensable de pilotage de la production.
Pour améliorer leur compétitivité ou leurs marges, toutes les usines souhaitent améliorer leur production. Mais peut-on améliorer sans mesurer ? Certainement pas. Or sans logiciel de MES, mêmes des mesures simples, telles que les temps d’arrêts ou les consommations de matière, vont mobiliser des temps et des ressources importantes sans grande fiabilité. Et que dire des mesures portant sur des opérations qui ne durent que quelques minutes, voire beaucoup moins. Comment assurer la traçabilité fiable exigée par les consommateurs ?
En réalité, seul le MES permet aux industriels d’être réellement crédibles et compétitifs dans le monde d’aujourd’hui.
La situation du MES est en fait similaire à celle de l’ERP. En toute objectivité, les décideurs des entreprises analysent-ils le ROI d’un ERP avant d’en faire l’acquisition ? Non, en réalité ils savent que se doter d’un ERP est indispensable à leur développement, et ils recherchent le logiciel le mieux adapté à leur métier et bien sûr, à leurs capacités financières.
En fait le problème n’est pas de savoir s’il faut ou non mettre en place un MES, mais quand !
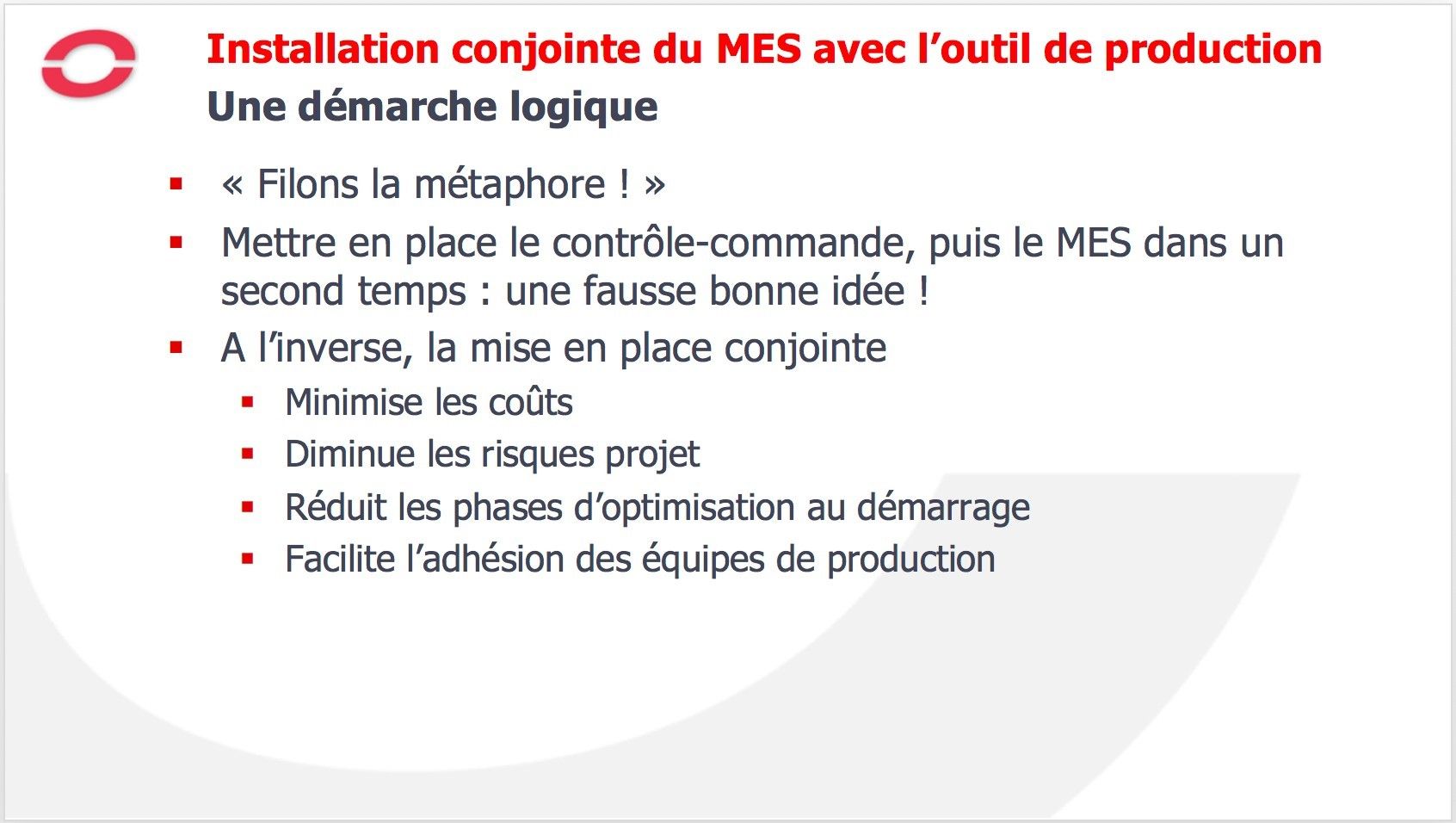
Filons la métaphore, comme le dit l’expression consacrée. Reprenons le cas de notre avion, ou plus près de nous, de la voiture : va-t-on dans un premier temps acquérir une voiture sans tableau de bord, rouler quelque temps, puis faire un nouveau projet de manière à disposer enfin d’un compteur de vitesse, d’une jauge d’essence et d’une centralisation des informations de pression des pneus ? Bien sûr, ce n’est pas le cas, et la sélection du tableau de bord est faite en même temps que l’achat du véhicule.
Y-a-t-il une raison de faire différemment pour un outil de production ? Mis à part le fait que l’acquisition d’un MES n’est pas encore aussi « naturelle » que celle du tableau de bord de votre voiture, pas vraiment !
En fait, privilégier la mise en place de l’outil de production, puis du MES dans un second temps, relève de la fausse bonne idée :
- En retardant sa mise en place, on retarde le retour sur investissement du MES
- On est conduit à la mise en place de solutions d’appoint « jetables » pour satisfaire les exigences (par exemple de traçabilité ou de qualité)
- Non pensé au départ, l’adéquation du MES au processus de production sera plus complexe
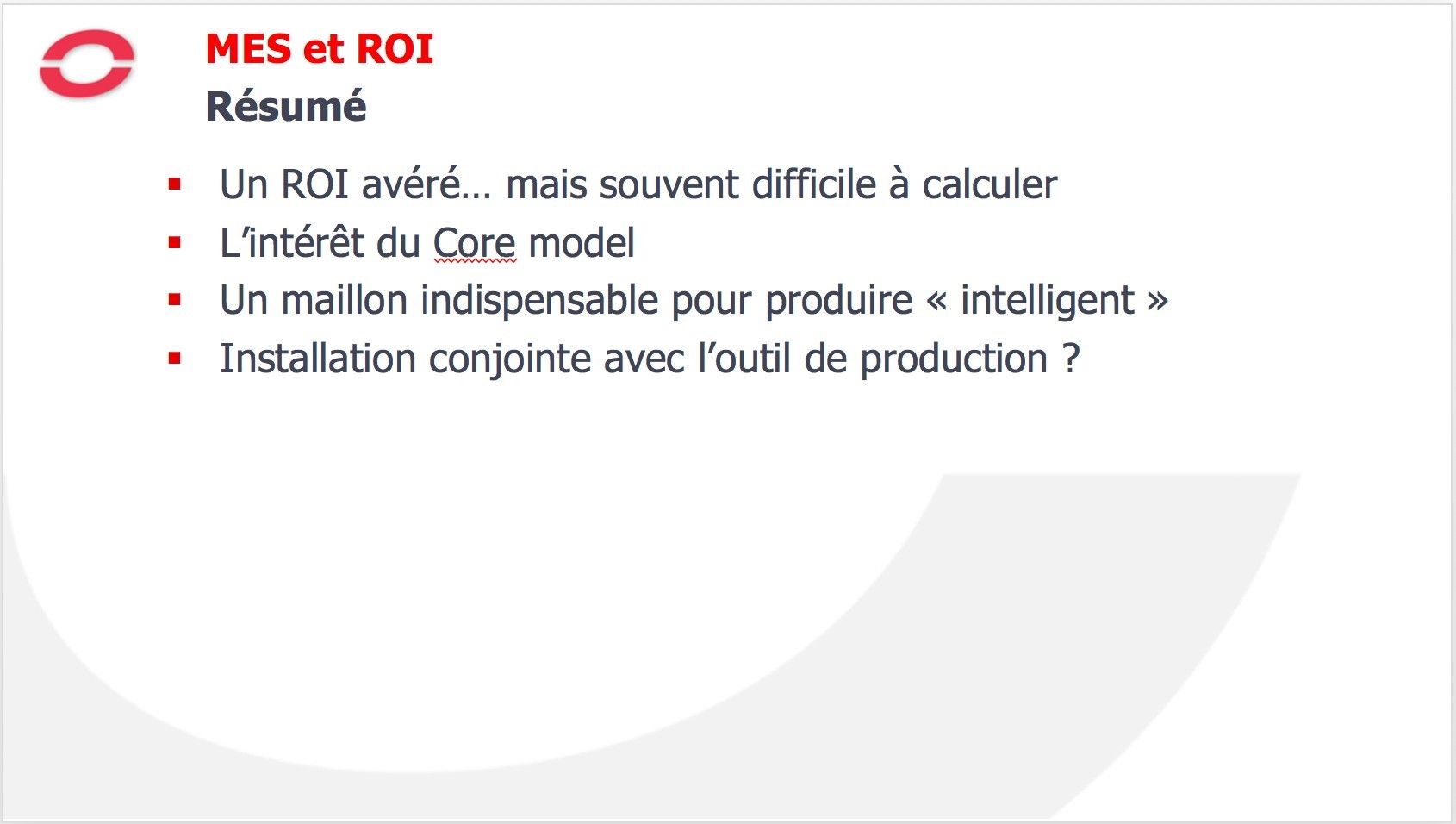
Je vous propose de résumer ce que nous avons vu aujourd’hui sur ce dernier thème.
On demande souvent au projet MES de justifier son ROI avant sa mise en place. Nous avons vu que si ce ROI est indéniable, et que même des pistes de calcul peuvent être données, cette justification du projet MES peut être délicate et n’est pas forcément la meilleure.
Sur le plan particulier d’un projet multi sites, nous avons également vu tout l’intérêt d’une démarche core model, qui permet la capitalisation d’un site à l’autre.
En approchant le problème différemment, nous en sommes arrivés à la conclusion que le MES est en fait incontournable pour produire intelligemment, et que le mieux est de mettre en place le MES le plus tôt possible, et nous avons vu tous les avantages de son installation conjointe avec l’outil de production.