Si l’on reprend la signification même du terme MES - Manufacturing Execution System – soit système d’exécution des fabrications, assurer de façon optimale l’exécution du plan de production ou plan de fabrication est l’une des principales tâches, sinon la seule, d’un système MES, et les différentes fonctions comme la traçabilité du procédé, des flux de matières, la mise en place et le suivi d’indicateurs de performance en constituent en fait des sous-ensembles.
La session d’aujourd’hui est donc très importante.
Après avoir déterminé de quoi il est question lorsque l’on parle de plan de production ou plan de fabrication, nous verrons les différentes méthodes qui s’offrent à l’industriel pour l’exécuter et pour le contrôler au travers d’un système MES.
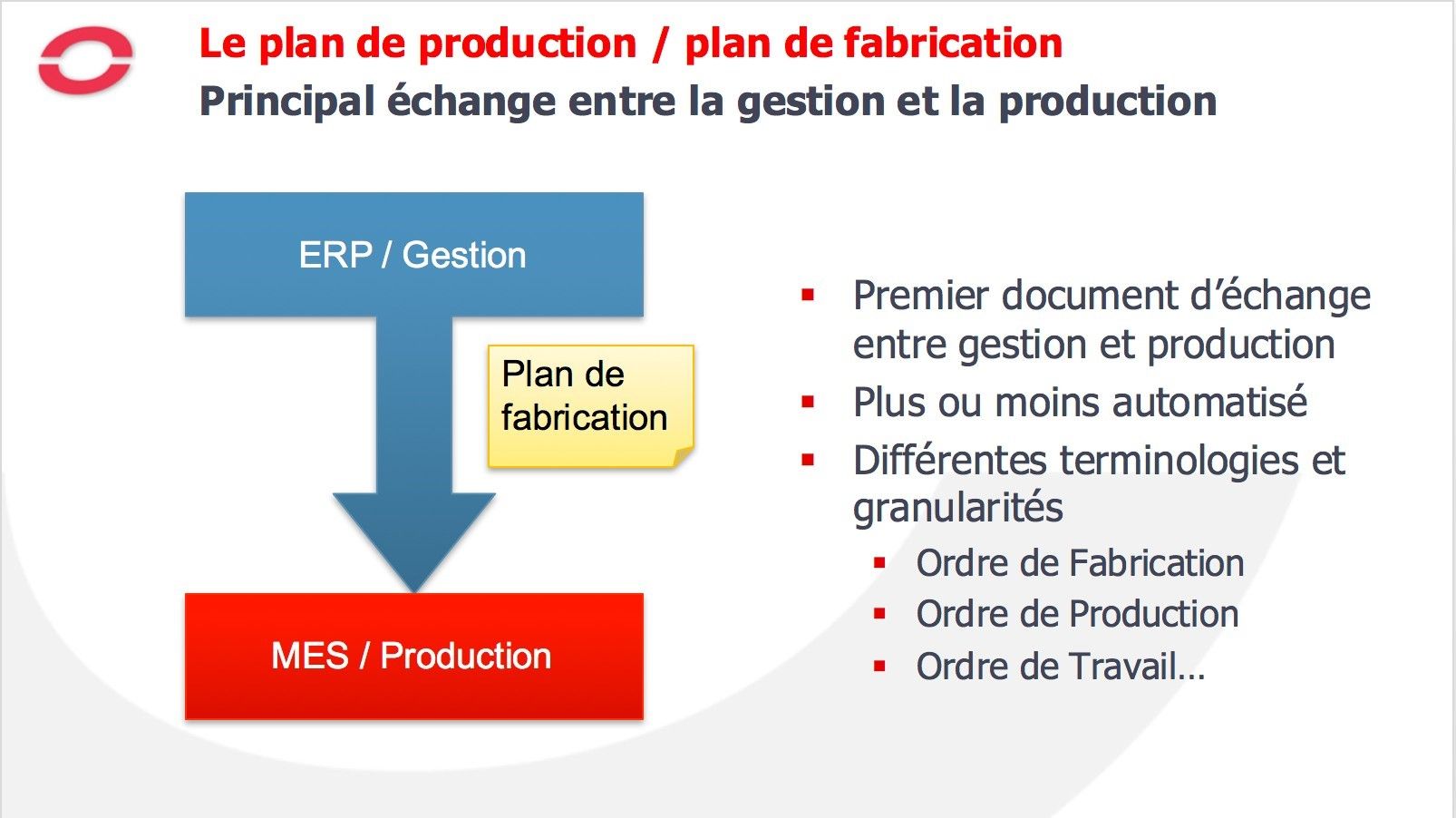
Tout d’abord, le plan de production ou plan de fabrication est le principal document d’échange entre la partie gestion de l’entreprise (généralement l’ERP), et la production proprement dite, au travers du système MES. Les échanges entre ERP et MES ont été vus en détail dans notre leçon n°2, que l’on pourra revoir à cette occasion. Le plan de fabrication est évidemment un élément majeur de ces échanges.
Comme nous l’avons vu, cet échange repose sur différentes technologies (fichiers, bases de données, échanges XML, services web) et il pourra être plus ou moins automatisé. A un extrême, le plan de fabrication est un document papier édité par l’ERP, et l’opérateur va lancer manuellement l’exécution en séquence de chaque ligne du plan. Plus fiable et plus efficace, l’import manuel de ce plan de fabrication par le responsable d’exploitation ou le chef de ligne en début de journée ou d’équipe. A l’autre extrême, le plan de fabrication est transféré automatiquement de l’ERP vers le MES périodiquement sans qu’aucune opération ne soit nécessaire.
Que contient ce plan de fabrication ? Le plan de fabrication est généralement organisé en lignes, chaque ligne étant planifiée à une date et une heure d’exécution, ou devant simplement être exécutée en séquence. Chaque ligne est en relation avec une commande client, ou un regroupement de commandes destinées à la fabrication du même produit. Suivant le procédé, les capacités de l’installation et celles du logiciel de MES, plusieurs lignes pourront être exécutées en parallèle.
Dans la pratique, on va rencontrer plusieurs termes pour désigner chacune de ces lignes. On parlera d’ordres de fabrication, d’ordres de production, d’ordre de travail. Suivant les industriels, ces termes désigneront en fait la même chose, ou des éléments de granularité différentes, permettant de passer d’une planification « macro » à une planification dite « détaillée ».
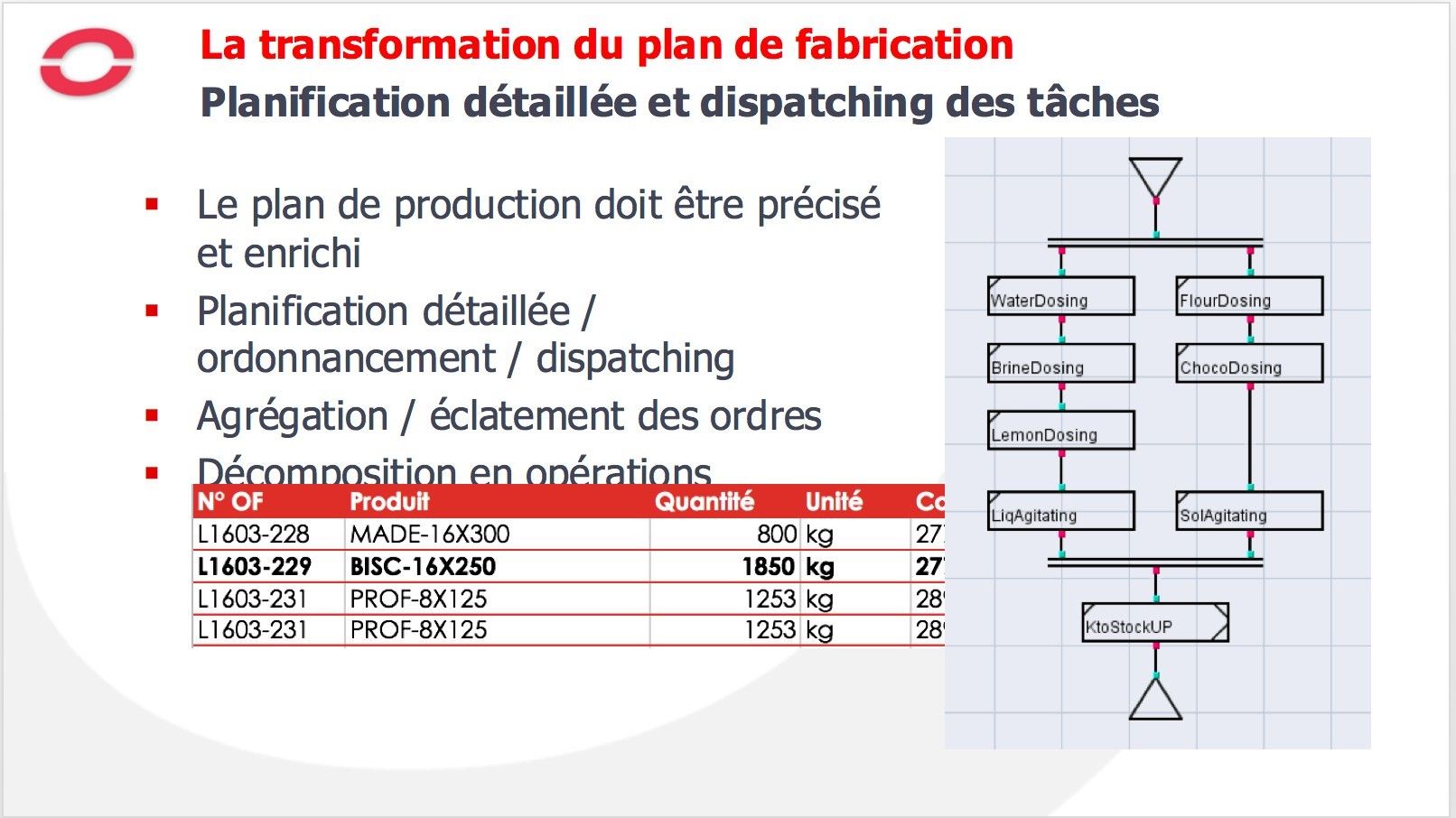
En réalité, le plan de fabrication issu de l’ERP est généralement un plan synthétique ou « macro », qui va devoir être enrichi pour en déduire une planification détaillée ou un ordonnancement, et ensuite être « dispatché » entre les différents sous- ensembles de production. Par exemple, la fabrication d’un produit va engendrer la production du produit lui-même, mais aussi celle de contenants et d’emballages. Cet enrichissement et ce découpage sont le plus souvent du ressort du MES.
L’ISA-95 distingue de ce fait deux activités distinctes pour cela : planification et dispatching, ces deux activités faisant appel à la gestion des ressources.
Par rapport au plan de fabrication initial, le MES devra également prendre en compte certaines contraintes. Par exemple, la quantité à fabriquer ne peut pas être faite en une seule fois : l’ordre de fabrication indique 1500l de peinture mais la cuve de mélange fait 1000l, il faudra donc effectuer la fabrication en deux fois.
A l’inverse, le MES peut être doté de fonctions d’agrégation qui vont permettre de regrouper en un même ordre de fabrication deux ordres qui concernent un même produit, permettant ainsi d’optimiser l’utilisation des équipements.
Une fois précisées les tâches à réaliser, celles-ci seront découpées en opérations, lesquelles peuvent être conduites en séquence ou en parallèle. Suivant les systèmes MES, cette décomposition pourra être plus ou moins profonde, formalisée graphiquement ou non, modifiable ou non en exploitation, et les conditions de branchement pourront être définies par paramétrage ou par codage.

Le maître mot de l’acronyme MES est Exécution. Et cela tombe bien, car comme cela est très bien démontré dans un livre écrit il y a quelques années, l’efficacité opérationnelle repose entièrement sur l’exécution. Ce livre ne traite d’ailleurs pas du MES, mais du management en général.
Comme l’exécution des fabrications s’appuie sur des hommes, mais aussi sur des systèmes logiciels et matériels, on peut dire que l’exécution des opérations repose en fait sur 3 composantes :
- Les opérateurs
- Les systèmes logiciels SCADA et MES
- Les automatismes
La répartition des opérations, sous-opérations et phases plus élémentaires d’un processus de fabrication varie grandement d’une industrie à une autre, et d’une installation à une autre pour une même industrie. De plus, si l’on distingue assez nettement les opérations manuelles et les opérations entièrement automatiques, il est plus difficile de distinguer des étapes qui sont réalisées au niveau de la supervision d’étapes faites au niveau du MES. Sans compter qu’aujourd’hui, de nombreuses étapes sont hybrides ou semi-automatiques : une pesée va nécessiter des actions manuelles de l’opérateur (poser le produit sur la balance et le retirer par exemple), tandis que le reste de l’opération (pesée proprement dite) sera effectué automatiquement sans que l’opérateur n’ait de saisie à faire.
Les choix de répartition des opérations entre les différents systèmes ne sont pas neutres, non seulement entre opérations automatisées ou non, mais aussi dans le choix du système qui exécute les opérations dans le cas d’une exécution automatisée ou semi-automatisée. C’est ce que nous allons voir avec la notion de moteur d’exécution ou de séquenceur d’opérations.
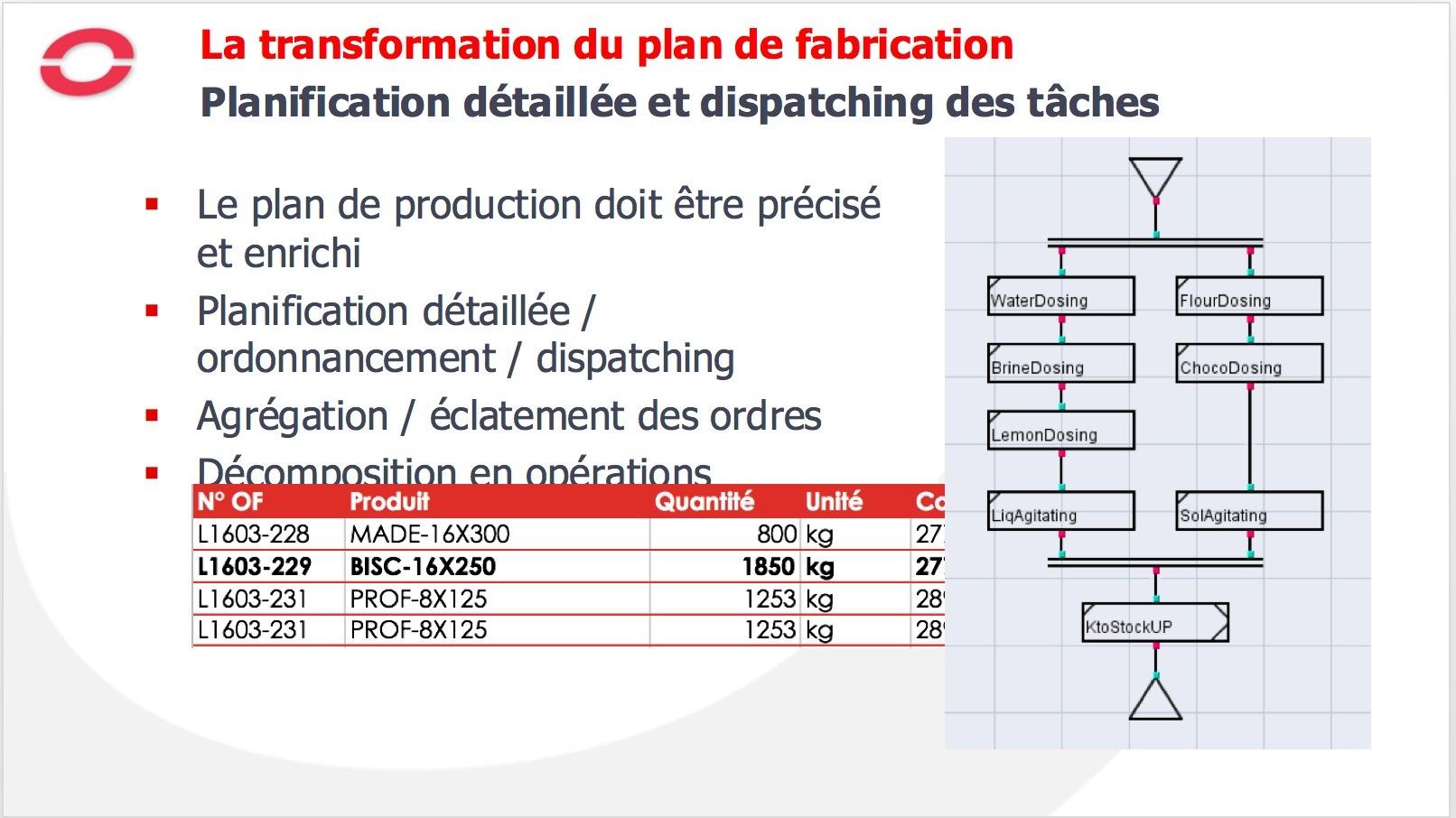
Ce schéma présente l’architecture d’une exécution automatique traditionnelle : l’enchainement des opérations est géré par les automatismes, éventuellement sous le contrôle d’une supervision.
L’ensemble du procédé se déroule en séquence dans l’automate. Pour paramétrer le procédé, la supervision envoie des « recettes de supervision » qui contiennent des listes de valeurs de paramètres. Dans ce type d’architecture, le MES est essentiellement un MES de suivi de l’exécution, ayant pour vocation de tracer certaines informations de progression des ordres de fabrication et des informations de performance.
Cette architecture présente l’avantage de la sécurité d’exécution :
- Les automates sont fiables, et présentent une grande sécurité de
- Côté automate, l’adaptation de paramètres permet dans une certaine mesure d’adapter les
- Côté Supervision, on utilise un outil éprouvé, et le dialogue avec l’automate est
Mais cette architecture présente tout de même certains inconvénients :
- La flexibilité des automatismes est réduite : si on veut changer l’ordre d’exécution des étapes, il faut modifier le programme automate.
- Si on doit répartir le procédé sur plusieurs automates, l’exécution est plus complexe : il faut transmettre la recette à un automate frontal qui va devoir synchroniser les autres automates.
- Côté supervision, on n’a pas de notion d’OF, d’ordre de lancement. Il faut donc un dialogue spécifique entre supervision et MES.
- Les étapes manuelles, généralement prises en charge par le MES, ne suivent pas le même « circuit » que les étapes automatiques (prises en charge par l’automate). Leur synchronisation est donc délicate.
- L’obtention d’une traçabilité fine (étape par étape) est complexe et délicate : l’accès aux différentes étapes d’exécution de l’automate représente une charge et un risque important pour le développement du projet. Elle est généralement abandonnée.
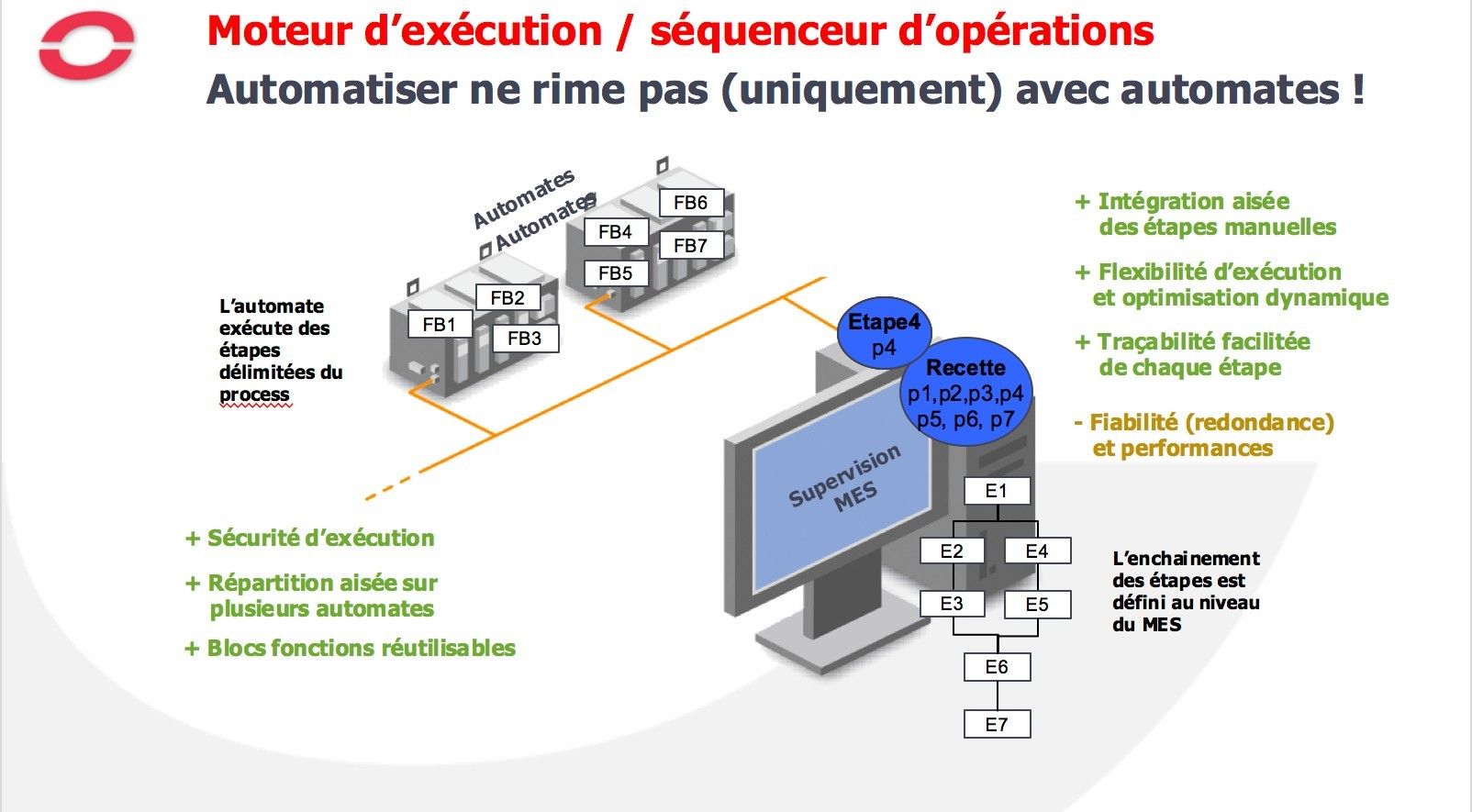
Certains systèmes de MES disposent d’un mécanisme d’orchestration des opérations, appelé séquenceur d’opérations ou moteur d’exécution. Dans ce cas, automatiser l’exécution ne rime pas avec automates programmables, en tout cas pas uniquement.
Ici vous voyez une architecture mettant en œuvre un moteur d’exécution.
Dans cette architecture, l’automate exécute des étapes délimitées du procédé, généralement réalisées par des « Blocs Fonctions » de l’automate. L’enchainement des étapes est défini au niveau du système MES.
Une recette comme celle que nous avons vu auparavant va cette fois se traduire par l’envoi des paramètres de chaque étape aux automatismes, directement ou au travers de la supervision.
Cette architecture présente aussi l’avantage de la sécurité d’exécution : c’est l’automate qui exécute intégralement chaque étape élémentaire du procédé. Un dosage, par exemple, va être maîtrisé de bout en bout par l’automate.
Dans le cas où l’architecture comporte plusieurs automates, il n’y a pas de complexité supplémentaire : chaque « bloc fonction » de l’automate correspondant est appelé en fonction de l’opération à réaliser. Plus simples et plus génériques, ces blocs fonctions peuvent d’ailleurs être réutilisés sur plusieurs lignes, voire plusieurs installations.
En revanche, les étapes de l’automate, ou d’ailleurs des étapes manuelles, peuvent être organisées depuis le système MES, sans nécessité de modifier le programme automate. Certains systèmes MES, disposant d’un outil de modification des séquences, permettent une modification de celles-ci en exploitation, sans modification de l’applicatif.
Suivant les systèmes de MES présentant ces possibilités, des algorithmes sont mis à disposition pour optimiser le déroulement du procédé : attente automatique qu’un équipement doit disponible, choix de l’équipement en fonction de critères dynamiques (quantité à produire, …), autant de traitements qu’il faudrait coder en spécifique dans le programme automate.
Les étapes étant cette fois connues au niveau du système MES, il est beaucoup plus facile de les tracer (date de début d’étape, de fin d’étape, paramètres,
...) et certains systèmes MES le proposent en standard.
Même si la sécurité est assurée par l’automate, dans la mesure où l’exécution du procédé repose cette fois sur le système MES, le point de vigilance est la fiabilité. Il faut donc des serveurs fiables pour le moteur d’exécution, et mieux encore un système de redondance qui permettra au système de repartir là où il s’était arrêté en cas de défaillance.

Une fois que le plan de fabrication a été exécuté, on souhaite généralement en connaître le résultat et les performances. C’est là aussi une des attentes clés du MES. Dans la pratique, on voudra connaître :
- Les quantités effectivement produites
- La qualité des productions
- Les durées de réalisation des ordres de fabrication, et généralement aussi les durées d’exécution de chaque étape
- Quelles sont les différentes ressources qui ont été utilisées : matières premières, équipements, personnel, pour chaque fabrication.
Ces informations vont généralement être retransmises à l’ERP, pour consolider ces informations et éventuellement pour affiner ses données de planifications, comme les durées standard d’exécution des opérations.
En parallèle, ces informations vont généralement être diffusées directement sous forme de rapports papier, éditions électroniques PDF, que l’on appelle rapports de production ou reporting de production. De plus en plus, ces informations seront également transmises à des outils d’exploitation analytique des données de type EMI (Enterprise Manufacturing Intelligence), intégrés ou non au système MES, qui permettent de multiplier les axes d’analyse.
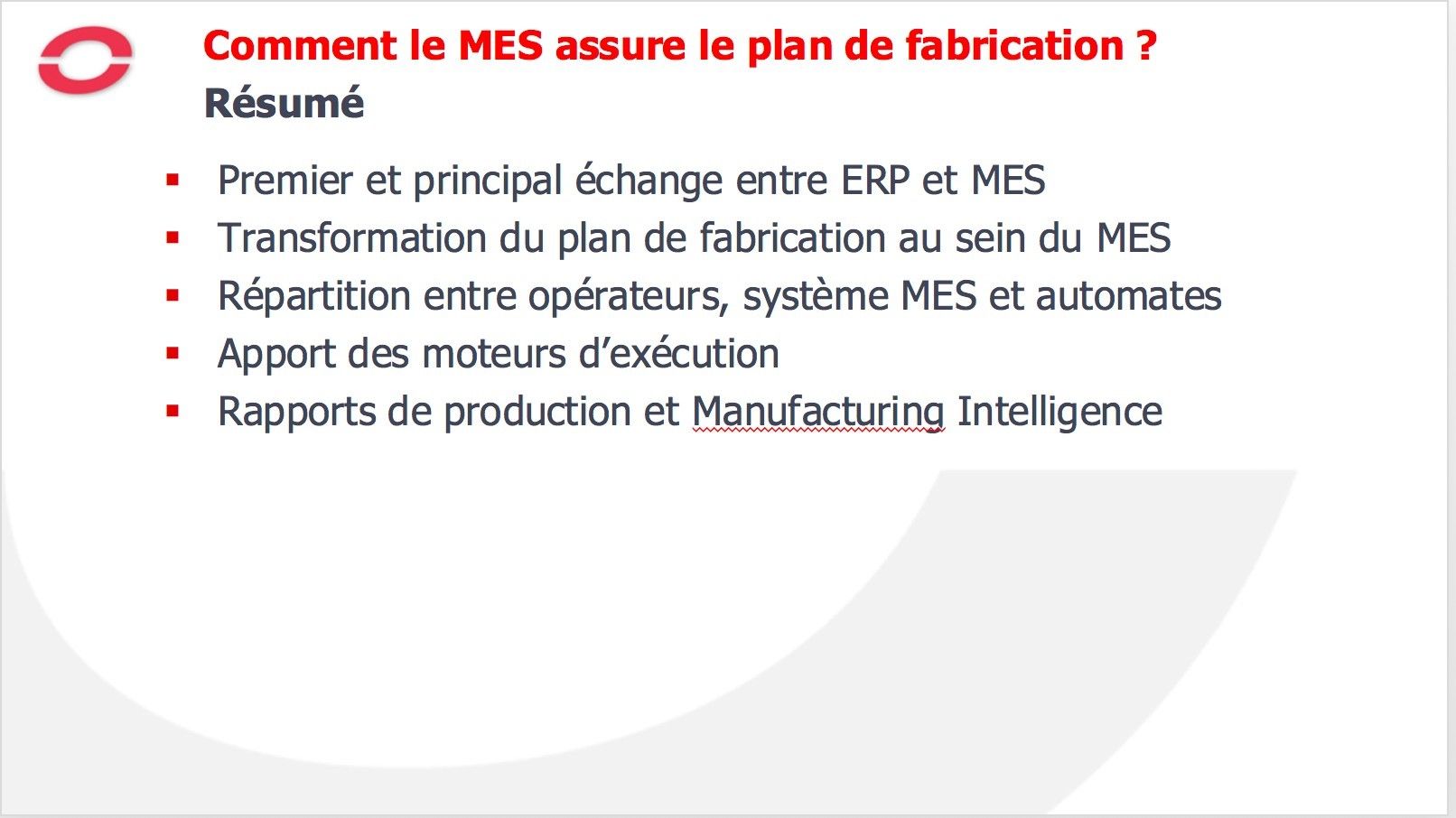
Un petit résumé de ce que nous avons vu dans cette session.
Tout d’abord, nous avons vu que le plan de fabrication est le premier et le principal échange entre l’ERP et le MES. Assurer le plan de fabrication est de ce fait l’une des principales attentes d’un véritable MES.
Nous avons ensuite constaté la transformation du plan de fabrication au sein du MES, en passant par l’ordonnancement ou la planification détaillée, le dispatching des tâches, puis d’exécution des recettes et des gammes.
Puis nous avons vu la répartition de ces opérations entre opérateurs, MES et automatismes.
Un focus a été fait sur les moteurs d’exécution, et leurs avantages en termes de flexibilité et de traçabilité.
Enfin nous avons vu qu’assurer le plan de fabrication, c’était aussi et dans certains cas surtout fournir les données de production au sein d’un rapport de production, voire permettre leur exploitation par la Manufacturing Intelligence