Portée par la 4ème révolution industrielle, la transformation digitale est en marche et doit faire face à de nombreux défis. Avec l'informatisation des usines qui ne cesse de s'accroître, un grand nombre de données critiques de l'entreprise sont amenées à se numériser (digitalisation des opérations) et doivent conduire les industriels à une vigilance accrue.
Ils doivent avant tout faire évoluer leur outil de production, se doter de systèmes de supervision et de MES fiables, ouverts et cohérents pour qu'ils puissent se connecter aux autres solutions déjà en place, et favoriser une bonne homogénéité de leur système d'information.
Comment peut-on, en effet, piloter une ligne de production qui s'adapte, en temps réel, aux cadences des postes de travail sans avoir réalisé auparavant l'interconnexion entre les différents équipements ?
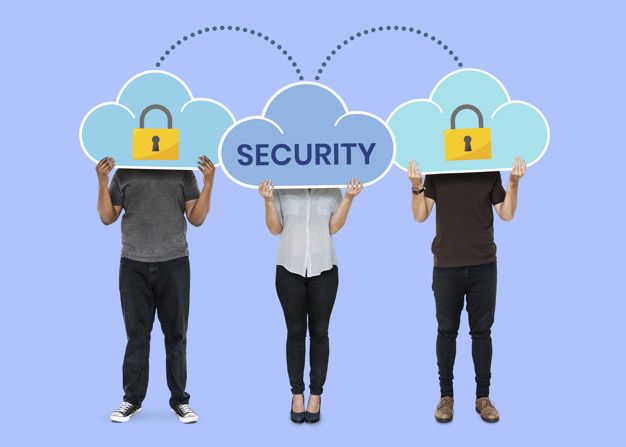
Dans un environnement où la compétitivité ne cesse de s'accroitre, les bénéfices à en tirer sont nombreux : gains de productivité, complexité supprimée, amélioration des capacités de production, meilleur service rendu à leurs clients...le temps passé auparavant à faire de la saisie sur des feuilles de papier ou dans des fichiers Excel ou Access peut ainsi être consacré à la résolution de problèmes, à une meilleure gestion des priorités ou même à l'amélioration continue.
Mais dans ce contexte, nous l'avons vu encore récemment dans l'actualité avec les cyber-attaques dans les hôpitaux, avec la fuite de données médicales de près de 500 000 personnes en France, la vulnérabilité de l'entreprise augmente.
La cyber-sécurité est essentielle et il existe déjà quelques bonnes pratiques à mettre en place sans tarder qui serviront de base à la sécurité de l'usine.
Parmi elles :
- s'assurer d'avoir un contrat de maintenance logiciel à jour afin de bénéficier des applications les plus récentes
- se doter d'une plateforme avec un OS supporté par l'éditeur : MS Windows, MS SQL Server mais aussi Ubuntu pour les logiciels compatibles à Linux.
- Avoir des applications protégées par des mots de passe.
La segmentation du système d'information apparait comme la technique la plus adaptée pour protéger son environnement. Sécuriser les automates et les postes de contrôle, isoler en cas d'attaque, et favoriser la communication entre la production et la direction des systèmes d'information.
La digitalisation de l'usine apporte des gains concrets et palpables au niveau de la performance de production. Elle est d'ailleurs bien souvent le pré-requis à d'autres évolutions internes et sert de passerelle à l'entrée dans l'ère 4.0 : Cloub, Big Data, IoT, réalité augmentée, maintenance prédictive, intelligence artificielle...mais il est primordial de sécuriser l'ensemble des systèmes (dans l'usine et à l'extérieur).