Souvent dévolu à la digitalisation des opérations de l'usine, au dispatching aux postes opérateurs des différentes tâches des ordres de fabrication issus de l'ERP et à la saisie des données de performance, le MES ne délivre pourtant tout son potentiel qu'en collectant directement les informations au niveau des machines.
Beaucoup d'usines récentes sont équipées de machines modernes et performantes, qui regorgent d'informations utiles dont leurs écrans de contrôle sont le reflet. Une aubaine pour les systèmes de MES ?
Pas si simple...
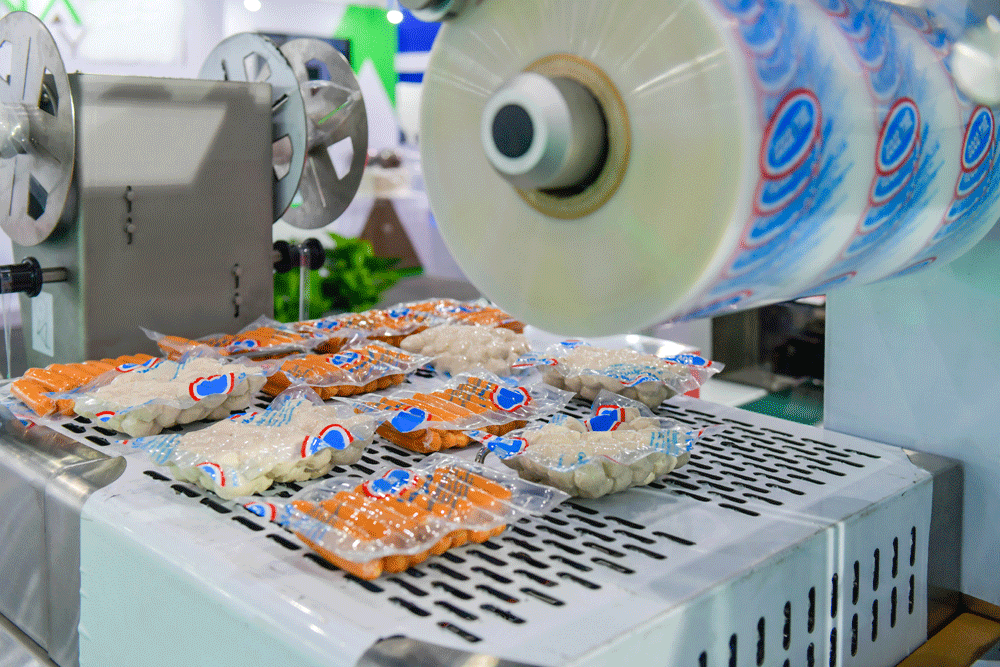
Les machines : un enjeu de capacité de production avant tout
Le choix d'une machine de production est un enjeu important pour l'industriel. Sa capacité à réaliser les produits à mettre sur le marché, les cadences qu'elle est capable d'atteindre, son confort d'utilisation, sa fiabilité, sa maintenabilité, la disponibilité des pièces détachées, les conditions contractuelles de maintenance, etc. sont autant d'éléments primordiaux que l'industriel doit prendre en compte, et qui vont décider de sa capacité de production pour plusieurs années. Tout cela en un temps relativement court, car le marché n'attend pas !
A ce moment, le suivi et l'amélioration de la production sont des enjeux plus lointains, et la connectivité de la machine entre rarement en ligne de compte dans les choix.
La machine choisie est moderne, les écrans de contrôle sont confortables et séduisent les opérateurs, que demander de plus ?
Parfois, l'atelier est lancé avec une seule machine menante, qui dispose de l'ensemble des informations nécessaires. Quel serait alors l'intérêt d'une connexion ?
Mais heureusement pour l'industriel, l'histoire continue. Le marché se développe, la capacité de production va devoir augmenter et l'atelier va voir grandir son parc de machines. Une véritable maîtrise du plan de production et des performances devient indispensable. Elle ne sera possible que par la mise en place d'une continuité numérique entre l'ERP et les opérations via le MES et une restitution en temps réel des performances de production. La collecte en temps réel des quantités réelles produites et rebutées, des temps d'arrêts et leurs causes deviennent un enjeu, et le problème de la connectivité aux machines refait surface.
Une stratégie perdant-perdant
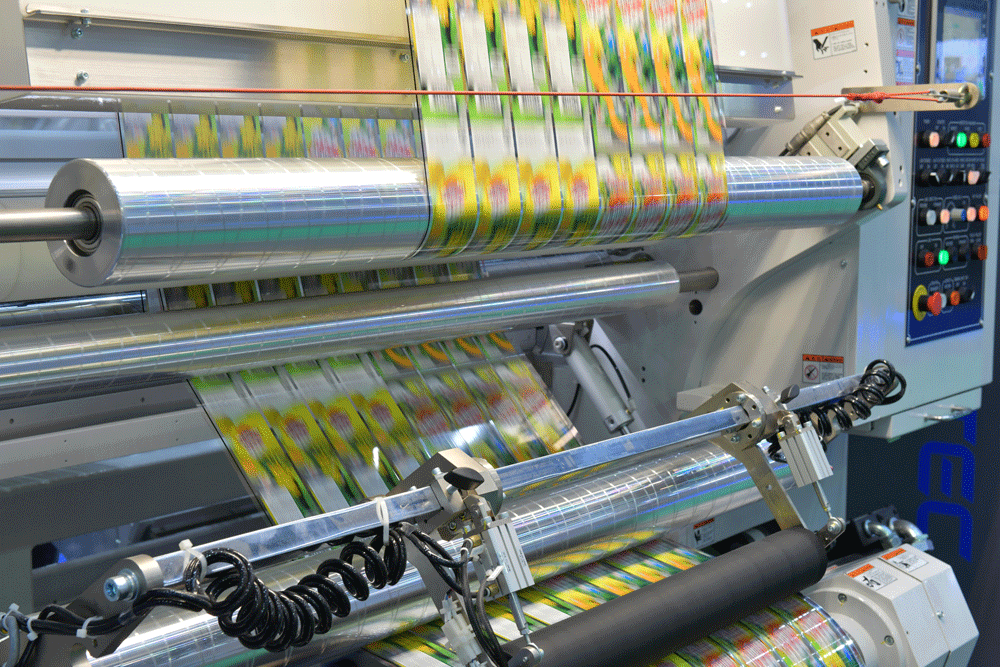
Bon nombre de constructeurs de machines vont pourtant complexifier cette connectivité nécessaire. En effet, alors que leurs machines sont dotées d'automates standards modernes ou de PC de supervision qui peuvent dialoguer aisément avec l'extérieur, ils en gardent secrètes les interfaces d'échanges, ou les proposent à un prix prohibitif, trop certains du fait que leur client est désormais captif, ne pouvant remettre en cause son investissement dont il est généralement satisfait par ailleurs.
Dans le même temps, certains développent et proposent un MES embryonnaire, système de suivi de production pensé en fonction de leur seule gamme de produits.
En résumé, plutôt que de faire de la connectivité de leurs machines un argument de vente dans le contexte de l'industrie 4.0, ils s'engagent dans une démarche propriétaire de vente quasi-forcée sans valeur ajoutée substantielle. Cette stratégie est pourtant vouée à l'échec : il est rare qu'un industriel dispose d'un parc homogène de machines d'un seul constructeur, et un MES propriétaire n'a que peu de chances d'être pertinent. D'un autre côté, la facturation des interfaces à un coût prohibitif a pour seul effet de reporter sine die la mise en place du MES chez l'industriel. Une stratégie perdant-perdant donc.
Le secours de l'IoT
C'est là que l'IoT entre en scène. Puisqu'il est difficile d'extraire les données disponibles dans les unités centrales des machines, pourquoi ne pas les collecter directement à la source ? La pose des capteurs nécessaires à l'obtention des informations souhaitées, par exemple, pour le calcul d'un TRS parfaitement fiable, ne nécessitera que quelques centaines d'euros. La MESbox QPI de COOX dispose d'un mode permettant de le délivrer à partir de trois informations seulement !
Plus prosaïquement, ce principe s'applique aussi à des systèmes d'entrées sorties déportées, qui pour la plupart disposent d'une interface TCP/MODBUS directement supportée par la plateforme COOX, car si les données internes des machines ne sont pas documentées, les entrées sorties électriques connectées aux différents capteurs de quantités passées ou d'arrêt/marche le sont généralement.
A bien y regarder, l'usage de l'IoT ou des systèmes d'entrées sorties déportées est même plus avantageux que d'accéder aux informations de l'unité centrale des machines, car ces dernières ne sont pas toutes formatées de la même façon, ce qui nécessitera un traitement différent pour chaque machine. Avec l'IoT, les flux d'informations peuvent être entièrement standardisés.
Finalement, un peu malgré eux, les constructeurs de machines auront stimulé la mise en place d'un MES de manière plus économique et efficiente, pour le plus grand bénéfice de leurs clients industriels.